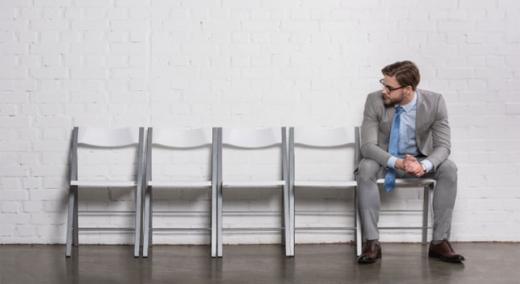
Manufacturing Day, an initiative designed to inspire the next generation of manufacturers, arrives Oct. 4, 2019. The annual MFG Day (which can be held anytime during the month) involves thousands of manufacturers across the country holding events, tours, activities, and more. Last year, in California alone, more than 250 sites registered as event hosts, and more than 330 manufacturers and support organizations participated in or sponsored events throughout the month of October.
ADVERTISEMENT |
One of the great benefits of participation in MFG Day is recruitment, which is vital to the survival of many of today’s small and medium-sized manufacturers (SMMs). Why is recruitment so important? Because today, nearly 90 percent of these manufacturers can’t find the employees they so desperately need, according to new data from SCORE, a nonprofit resource partner and mentoring service associated with the U.S. Small Business Administration (SBA).
…
Comments
Utilizing the Experienced Workers in the US
HOW DID WE GET HERE?
I have read a lot of articles lately discussing the coming retirement of the Baby Boomers, written by people who think everything now is "new technology" and robotics. Well, that day may be coming, but for most companies this "cutting edge technology" has not arrived yet. After years of scrimpy spending on infrastructure at most companies, they also don't have the capital to switch to new technology. In a nutshell, many manufacturing jobs are pretty much the same as they were before the huge outsourcing efforts of the early 2000's occurred.
Most companies are not interested in training new employees, they stubbornly offer wages that have not shifted for manufacturing employees in 20 years. It may be interesting to note that CEO pay has increased to over 390 times the pay of the lowest paid employee in US companies. The government believed that those jobs are never coming back. Well, surprise, they did, and management has not adapted to this new reality.
THE SOLUTION-FLEXIBILITY
The old time form of employment is not effective in todays market.
GIVE THESE NEW IDEAS A CHANCE. YOU WON'T REGRET IT.
Add new comment