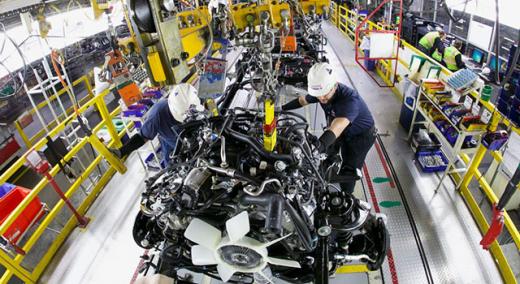
Recently, I came across an interesting insight at Toyota’s website. I was taken aback by the first sentence of this paragraph: “Eventually, the value added by the line’s human operators disappears.”
ADVERTISEMENT |
The complete paragraph is shown below:
“Eventually, the value added by the line’s human operators disappears, meaning any operator can use the line to produce the same result. Only then is the jidoka mechanism incorporated into actual production lines. Through the repetition of this process, machinery becomes simpler and less expensive, while maintenance becomes less time consuming and less costly, enabling the creation of simple, slim, flexible lines that are adaptable to fluctuations in production volume.”
Generally, we talk about increasing the value-added activities in lean or the Toyota Production System (TPS). Here, Toyota seems to be stating a paradox: We should get so good at what we do that we do not add value anymore. We keep finding better and better ways at doing what we do so eventually the process doesn’t necessarily need us to do that job.
…
Comments
Value added
What this says is simply that the concept of value-added as used in the Lean literature is half-baked and ill-defined.
See: https://michelbaudin.com/2012/02/02/occams-razor-value-added-and-waste/
Add new comment