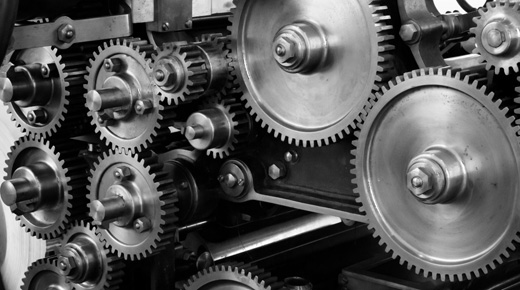
Mean time between failures (MTBF) is a symptom of a bigger problem. It’s possibly a lack of interest in reliability (which I doubt is the case). Or it’s a bit of fear of reliability.
ADVERTISEMENT |
Many shy away from the statistics involved. Some simply don’t want to know the currently unknown. It could be the fear of potential bad news that the design isn’t reliable enough. Some don’t care to know about problems that will requiring solving.
Whatever the source of the uneasiness, you may know one or more co-workers who would rather not deal with reliability in any direct manner.
Is ‘reliaphobia’ a thing?
Maybe not directly, yet the symptoms seem to be there. A mindset of avoidance concerning the topic, the lack of focus to understand or improve reliability, the dismissal of estimates or test results, the rush to “put right” any life limiting problems.
The general desire to move on or away from detailed discussions concerning reliability is a clue. This may be difficult for reliability professionals to grasp because we tend to enjoy understanding failure mechanisms. We tend to work to estimate or analyze reliability performance. It is what we do.
…
Add new comment