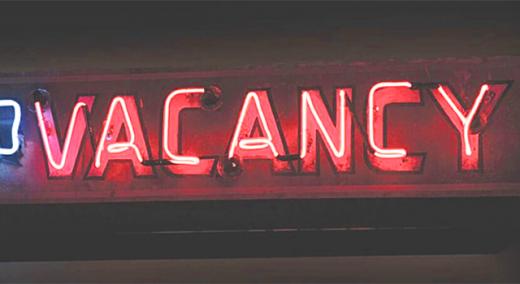
For those in the manufacturing and industrial sector, what’s commonly known as the skills gap is a well-documented issue. As a growing number of Americans retire, they take their decades of experience with them, resulting in a noticeable skills shortage.
ADVERTISEMENT |
The problem is poised to hit businesses hardest during the next few years, with more than one-quarter of the domestic manufacturing workforce over the age of 55.
The skills gap continues to widen
The manufacturing industry is already beginning to feel the impact of the skills gap.
“The retirement onslaught as we predicted is actually happening,” says Patrick Flaherty, an economist at Connecticut’s Department of Labor. “We’ve been talking about this for quite a number of years. You don’t have to be a genius. Just look at the age profile.”
…
Add new comment