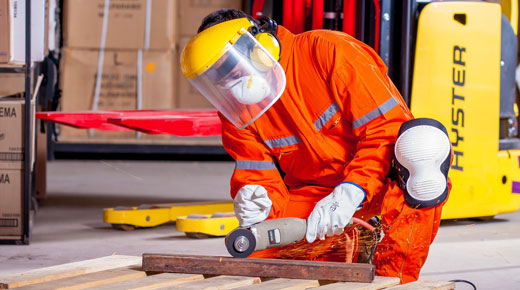
Chad Kymal1 gave an excellent overview of the ISO 45001 occupational health and safety (OHS) standard that was released in March 2018. I purchased a copy of the standard, and it provides an excellent framework, modeled on Annex SL, which defines the structure of all the new ISO standards, for an OHS management system. “Management system” is important because, although workplace safety has been mandatory for decades, traditional safety departments have the same limitations as traditional quality departments: The activity in question is limited to an organizational silo, as opposed to being part of a comprehensive and integrated management system.
ADVERTISEMENT |
Kymal’s webinar pointed out that ISO 45001 is not prescriptive. It does not include product safety (a separate issue from workplace safety) or even OSHA requirements, although it is emphatically synergistic with OSHA requirements, including those for OSHA’s voluntary protection program (VPP).
…
Add new comment