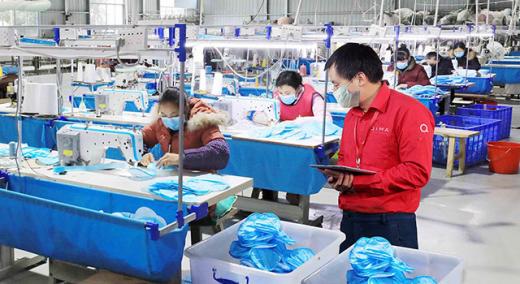
It’s been about one year since the Covid-19 impact intensified from a seemingly isolated health scare to a worldwide, ubiquitous tragedy that has upended daily life as we know it. Ever since consumers first faced widespread product shortages of essential items during the early days of the pandemic, ranging from toilet paper to medical supplies and PPE, there has been an unprecedented spotlight on supply chain management.
ADVERTISEMENT |
Although much of the conversation has focused on responding to waves in supply and demand, supply chain data suggest that the pandemic is triggering long-lasting supply chain trends that present both pros and cons for quality measures in supply chains.
…
Add new comment