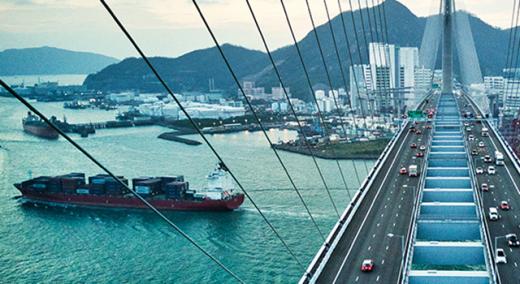
Body
In recent months, the widespread lockdowns of Covid-19 have exposed global supply chains to unprecedented shifts and volatility in consumer behavior, impacting innumerable organizations, industries, and consumer goods. While much of the supply-chain overhaul conversation has focused on drops in demand and disruptions in business across various consumer categories, delivering on sharply rising demands for medical equipment has been particularly challenging for companies in the healthcare manufacturing space.
…
Want to continue?
Log in or create a FREE account.
By logging in you agree to receive communication from Quality Digest.
Privacy Policy.
Add new comment