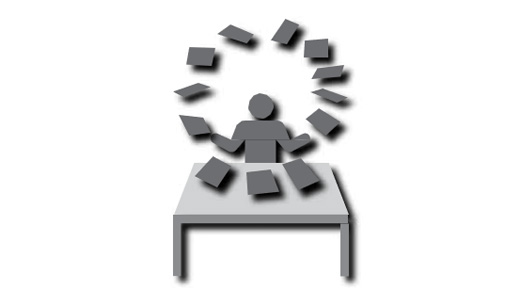
There is a proliferation of management system standards and requirements globally. These management system standards are either customer or industry mandated. Many standards are becoming a requirement for doing business.
ADVERTISEMENT |
For example, ISO 9001 is a quality management system (QMS) standard with industry-specific versions such as IATF 16949 for automotive, ISO 13485 for medical devices, and AS9100 for the aerospace industry. ISO 14001 is an environmental management system (EMS) standard, and ISO 45001, an occupational health and safety management system (OHSMS) standard. All of these either already are, or are quickly becoming, threshold standards for doing international business.
There are yet other standards waiting in the wings that may soon become industry requirements for social responsibility or sustainability, laboratory management systems, and energy management systems. Typically, these standards are seen as hindrances or obstacles in the way of doing business and therefore not beneficial.
…
Comments
IMS for ISO (or other QMS) Requirements
Often the problem is not the integration of the systems. Often the problem is one of organizational diversity. At the implementation level the organization is typically stovepiped into specialties where the individuals who are separately tasked with implementation of these management systems may not even be in the same state, let alone the same building. A quality control manager implementing QMS may not even be aware that there is a corporate health scientist implementing OHSMS.
While someone at the executive level may be in a position to see the need for IMS on an intellectual level, they are so far removed from the actual tasks that they may never see the actual cost that the organization bears by not doing so. Therefore it may never become a priority for them to implement IMS. Meanwhile, quality professionals become overwhelmed with duplicative reporting requirements.
Add new comment