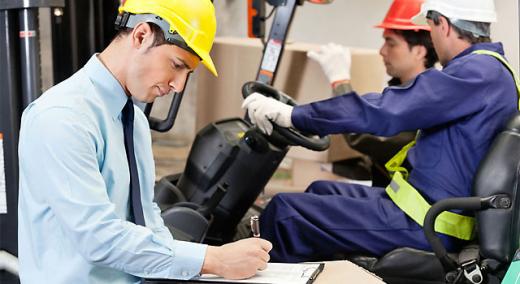
Starting a new facility in the food-processing industry is an enormous undertaking. There are thousands of things that must be accomplished, from hiring and training new staff to ordering and installing equipment. This scenario is a perfect example of “too much to do and not enough time to do it.”
ADVERTISEMENT |
To further complicate the situation, most customers require one or more audits of the site’s food safety quality (FSQ) system before the first sellable product can be produced on the line. These qualifying assessments range from a casual, on-site visit by the customer to a global food safety initiative (GFSI) audit.
Meeting the ever-increasing standards of something as daunting as a full-blown GFSI audit can be an intimidating prospect, and success can be achieved only through strategic planning. There is so much to be done to get the plant running before looming deadlines, which often leaves little time to prepare for initial audits. This is a race against the clock, but success is possible through alignment, engagement, planning, and prioritization.
…
Add new comment