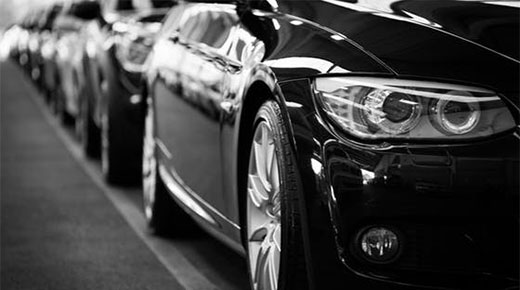
The Automotive Industry Action Group (AIAG) and the German Association of the Automotive Industry, or VDA (Verband der Automobilindustrie), have been cooperating in automotive quality management systems since the advent of the second edition of ISO/TS 16949 in 2002. The integration work that started with ISO/TS 16949 naturally evolved into an integration effort of the failure mode and effects analysis (FMEA) standards. The two FMEAs are quite different from each other in approach. Some of these differences will be illustrated in this article.
ADVERTISEMENT |
The current work is the outcome of three years of collaboration by a team of AIAG and VDA FMEA stakeholders. These comments are based on the draft document released for public comments on Nov. 27, 2017. It is assumed that the final release will incorporate these and other suggestions.
…
Comments
Process Flow, P-FMEA, CP and Workinstruction
All this documents belongs together, also at the VDA-Group. Your statement is wrong. The VDA concept is good, but the current description is bad. Seams that beginners in FMEA have written this paper. They think maybe more pages are better, but the opposite is the true.
Add new comment