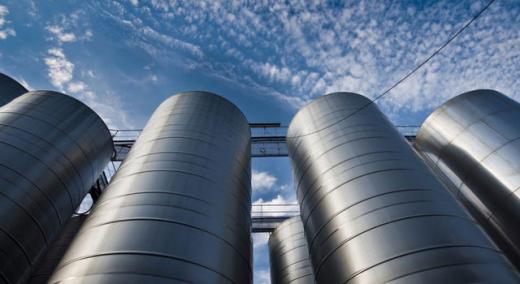
PDCA—plan, do, check, act (or adjust)—is one of those acronymic concepts that regularly finds its way into lean discussions. Descended from Francis Bacon’s scientific method (hypothesis, experiment, confirmation), PDCA has become a ubiquitous catchword for business process improvement. From standardization and problem solving on the frontline to iterative product and process design to hoshin, this approach is the engine for continuous improvement.
ADVERTISEMENT |
But like many lean concepts, when layered over a traditional organizational structure, PDCA can fall far short of its promises.
My initial exposure to the concept, Shigeo Shingo’s Zero Quality Control: Source Inspection and the Poka-Yoke System (Routledge, 1986) offered an unusual, nontechnical insight into PDCA. Referring to the concept in the context of quality improvement as “informative inspection,” Shingo posed a couple of critical questions:
1. How rapid is the feedback?
2. Who is involved?
…
Comments
When PDCA Meets Silos
Agree with all the points and quotes. Valuable. However, there is a real reason why Dr Deming changed PDCA (Please don't change anything in some vernacular) to PDSA. Ford Motor Coy found that people were ''checking' quality with the go-no gages and that was fine on the lines but in essence inn using the Shewhart/Deming Control Charts, Ford queried Deming to request could they change Check to Study. This is what I was told by Ford and in either ex-President Caldwell or Petterson's books. Pyzdek explains it well too in Six Sigma Handbook. Dr Deming as I was told and paraphrased "PDCA was attributed to Dr Shewhart, it is his, not mine, yes PDSA reflects the Study of the process behavior / control chart to learn what the process is doing and to do nothing or take action on the process as Dr Shewhart and I said and trained you in his CC's, to assure stability before capability'.
I have a copy of the CWQC For Automotive Suppliers report written by LP Sullivan Ford MC Dearborn MI June 1985 and in Stage 3 QA Involving all departments pp48-49 "In many U.S. companies there is a significant inhibition to the more successful use of the quality team concept: strong vertical departments with separate performance objectives. When Dr Ishikawa was here in May 1983 he pointed out how U.S. companies are typically very strong vertically and somewhat weak horizontally; this characteristic effectively prevents the natural development of CWQC. He likened it to weaving cloth and why U.S. management does not understand this! The essence of Japanese style CWQC is to deploy the 'Voice of the Customer' horizontally through e company ; not vertically". My dear departed friend Dr Howard B Aaron Q.E.D. West Bloomfield Mi presented me this HB when in Sydney for the BHP QFD/Taguchi sessions for our largest steel manufacturer BHP Rod and Bar Division Newcastle NSW Australia.
Add new comment