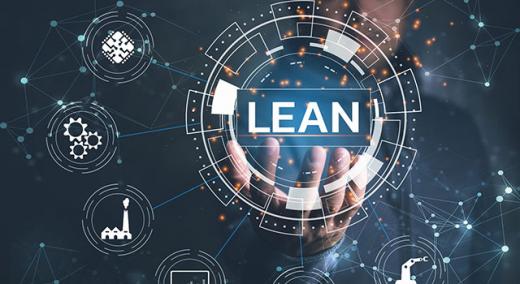
In the first article of this series, we saw that Lean and Six Sigma are complementary continuous improvement methodologies that reduce the overall waste and variability in production processes, respectively. Although these two methodologies use different approaches and tools to drive improvements in productivity and profitability, they have in common that they can be employed to improve every facet of your business. In this article, let's explore the principles and tools of lean.
ADVERTISEMENT |
Lean philosophy
Lean pillars
Lean philosophy has two interconnected pillars, eliminate waste and respect for humanity. These foundational elements greatly contribute to the success of lean manufacturing. Let’s talk about them individually—the second one first.
…
Add new comment