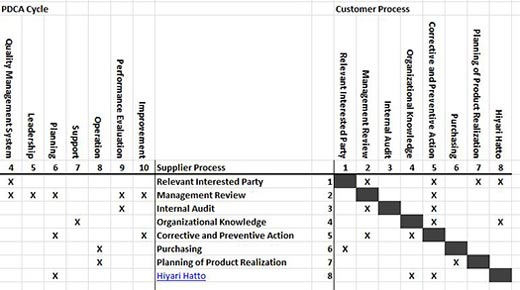
Among other requirements ISO 9001:2015, clause 4.4.1 requires an organization to identify the inputs and outputs of the processes of the quality management system; identify the sequence and interaction of these processes, noting that handoffs between processes often create risks; and identify the resources required by the processes. These provisions are consistent with the supplier, input, process, output, customer (SIPOC) model that treats processes as internal customers and suppliers.
ADVERTISEMENT |
This article recommends the SIPOC conformity matrix as a centerpiece of a quality manual that serves as a centralized information source for management and auditors.
The fact that ISO 9001:2015 does not require a quality manual does not mean, of course, that a first tier document that describes the entire quality management system (QMS) is not extremely useful. It is a good place to identify the context of the organization (clause 4.1), relevant interested parties (4.2), the scope of the QMS (4.3), the quality policy (5.2), and possibly the performance metrics, inputs, and outputs of the management review (9.3). This tells an auditor or other relevant interested party up front what your organization considers important.
…
Add new comment