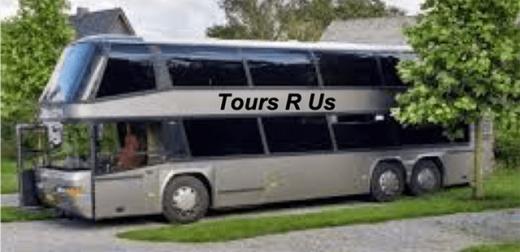
After being recognized in 1990 by the Shingo Prize, my plant became an overnight hot spot for benchmarking. Hardly a week went by when there was not a visit from a distinguished visitor, Fortune 500 company, professional organization, or college class. Initially, we accepted the visits because of the good publicity for the company; good news sells products.
ADVERTISEMENT |
But very quickly we discovered that the process of sharing our continuous improvement story had a powerful effect on our employee and management commitment to lean. This was not an outcome that I had anticipated.
…
Add new comment