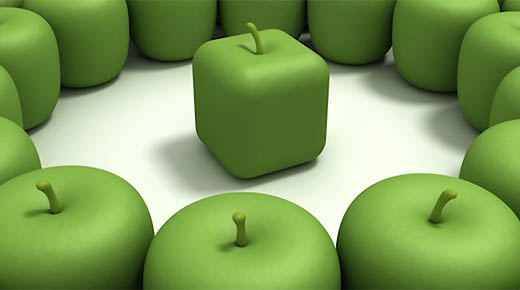
Body
The first two books I ever read about lean were Zero Inventories (McGraw-Hill, 1983) by Robert Hall, and Japanese Manufacturing Techniques (Free Press, 1982) by Richard Schonberger. In 1985, these definitive academic works were among just a few sources of information about what was then referred to as “just in time,” or JIT for short.
ADVERTISEMENT |
…
Want to continue?
Log in or create a FREE account.
By logging in you agree to receive communication from Quality Digest.
Privacy Policy.
Add new comment