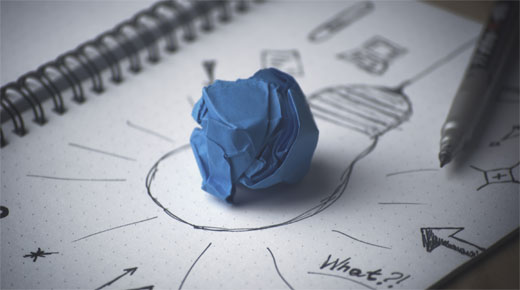
Labor costs are likely the largest line item on your company balance sheet. Therefore, a successful cost-reduction strategy must adequately balance resourcing and cost controls.
ADVERTISEMENT |
Although laying off part of the workforce may seem like the quickest and easiest solution to reducing labor costs in manufacturing, it may not be the best way to resolve the issue. The cost of finding and training new employees is extremely high, so it makes more financial sense to hold on to your employees and keep them happy.
But this begs the question, “is there a way of reducing labor costs in manufacturing without laying off the workforce?” Luckily, there are several. Here are six methods for reducing labor costs in manufacturing:
1. Cost reduction by design
Product development drives about 80 percent of the product’s cost. Of that cost, the concept and program architecture drive about 60 percent. Therefore, manufacturers can save a significant amount of money on parts, materials, quality, and labor by considering cost reduction during the design phase of the product.
…
Add new comment