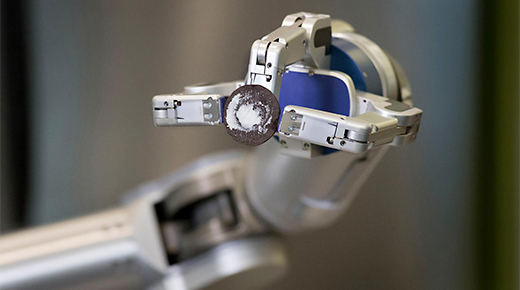
Speaking at the 2003 Shingo Conference, Guy Briggs, general manager of North American operations for General Motors lamented, “We spent the 1980s ‘counting robots’ before we realized that it’s people that make the difference in our business.”
ADVERTISEMENT |
He was alluding to the thirty-five billion (yes, billion) dollars that GM had invested in the 1980s over a three-year period to develop “lights-out” robotics technology. As Toyota sought to elevate employees, GM tried to automate them out the picture. Ultimately, GM’s lights-out peopleless “flexible manufacturing systems” were deemed unworkable and were mothballed. All told, GM spent 90 billion dollars in the 1980s to “modernize” its operations, touted by many as Industry 3.0, the third industrial revolution. At the beginning of that revolution, GM was the lowest cost U.S. auto supplier. By the end, it was the highest. The greatest shame in this saga was not so much the money squandered on equipment, but time lost by adopting the wrong philosophy: one that idolized technology while disrespecting people.
…
Add new comment