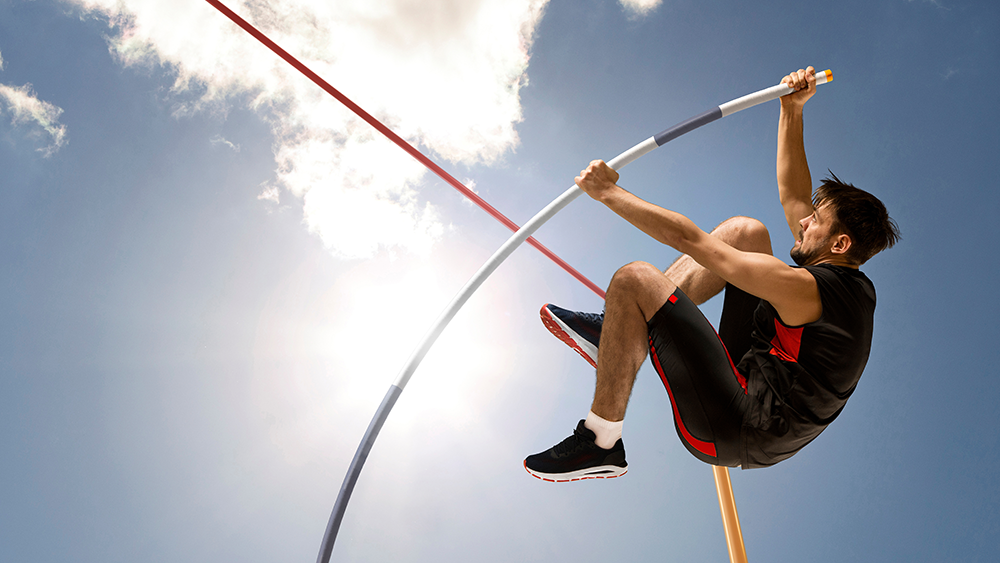
Adobe
One summer when I was a kid, my friend Rick and I built a pole vault setup in my postage stamp-sized backyard with a plant box (the place where you plant the pole as you begin your vault) and a couple uprights to hold the crossbar. We used bamboo poles acquired from a local carpet store for both the crossbar and the pole vault pole. The pit consisted of a couple old pillows—good enough for 12-year-old beginners.
ADVERTISEMENT |
During the months of July and August, we wore out a path in the grass and the skin on our elbows as we tried and failed to clear the bar. To try this event is to appreciate the number of things that have to go right simultaneously. Our only source of information was a chapter from a book on track and field events. But by summer’s end, bruises and all, we were both able to clear a height of six feet.
…
Add new comment