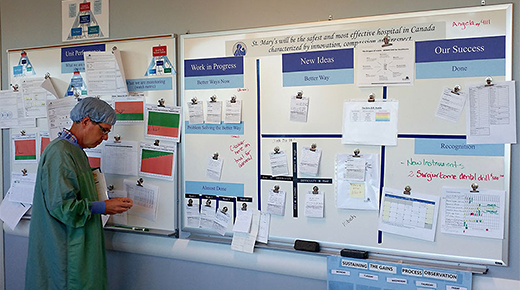
Body
Many years ago, the Toyota Production System Support Center (TSSC) introduced a visual measurement device to my factory, referred to as a “production activity log” (PAL), also known to some as an hour-by-hour chart. Posted at the last operation of a particular process, the PAL provided an up-to-the-minute accounting and hourly summary of actual production quantity vs. plan.
ADVERTISEMENT |
…
Want to continue?
Log in or create a FREE account.
By logging in you agree to receive communication from Quality Digest.
Privacy Policy.
Add new comment