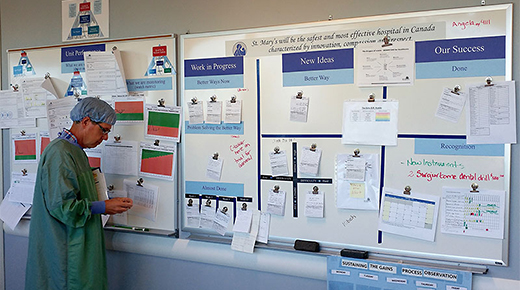
Three years ago I wrote an article titled “The Emperor’s New Huddle Boards,” in which I expressed concern about the trappings of improvement without actual improvement. Since then, my concern about the application of leader standard work and gemba walks has deepened as these potentially valuable practices have too often degenerated into obligatory, scripted play acting.
ADVERTISEMENT |
Ten years ago, when I first heard David Mann presenting these concepts, I thought to myself, “Hm, it’s about time that someone gives thought to the best use of managers’ time in support of kaizen.”
…
Add new comment