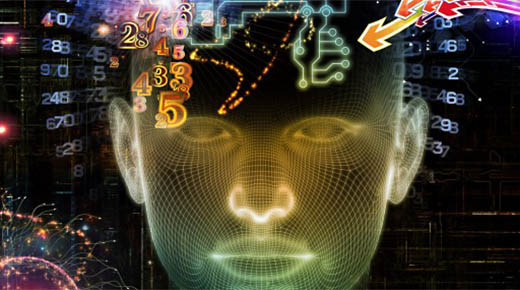
Who remembers VisiCalc, often referred to as the first killer app? In 1978, this spreadsheet software ushered in the personal computing boom. Although it only ran on Apple’s priciest computer (the one with massive 32K RAM), its ability to calculate and recalculate arrays had much to do with the explosion of information automation.
ADVERTISEMENT |
By 1985, a next-generation product name Excel conquered the market with significantly more computing capability than its predecessors, eventually adding macros, graphics, nested arrays, and easy interface with many other applications. Today Excel is reportedly in the hands of some 1.3 billion users. It’s a fascinating tool with more features than almost anyone can use.
…
Add new comment