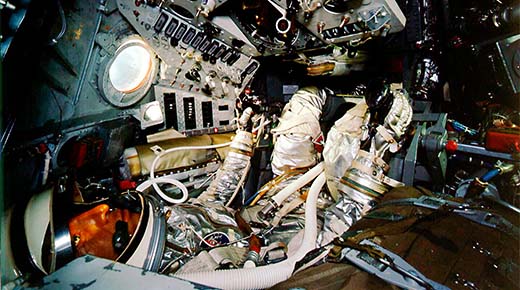
On May 5, 1961, Alan Shepard became the first U.S. astronaut to journey to the “final frontier.” Atop a Mercury rocket, Shepard launched into a 15-minute suborbital journey reaching an altitude of about 100 miles before returning to Earth. His space capsule, Freedom 7, was a wonder of science, weighing a little more than one ton and loaded to the max with avionics and life-support apparatus.
ADVERTISEMENT |
Yet, this pioneering venture into endless space would also afford almost no space for the passenger. According to launch engineer Guenter Wendt, “Astronauts entered their capsules with a shoehorn and departed with a can opener.” I remember watching footage of Shephard squeezing into his capsule. The memory still creates pangs of claustrophobia.
Ironically, space constraints faced by NASA fueled a revolution in miniaturization evident in almost every innovation of modern society—from laptops to cell phones to transportation to medical devices to all things internet. The need to pack more utility into a small package has changed everything. Or almost everything. Here are some recent exceptions:
“We’re adding a new wing to manufacturing,” a colleague related to me recently. “We’re running out of space.”
…
Comments
Gut Feel Often Trumps Analysis
I worked with one chemical company that kept key materials in a warehouse 1/2 mile from the plant.
I worked with a printer that kept glue for a binding machine three football fields away.
Sensei asked one hospital, "What are all the open spaces were in the hospital?" "Waiting rooms."Sensei asked, "Who waits there?" "Patients." Sensei asked, "How long to do they wait there?" "45-60 minutes." Sensei asked, "Aren't you ashamed."
When I worked in the phone company, the outside plant people thought they needed more people to handle telephone repairs. I asked, shouldn't we just reduce the need for repairs?
As problems become more complicated, gut feel is usually wrong. A little analysis will save a ton of money and time.
Transformation of Perception
Hi Bruce,
I picked the following quotes from your piece:
“This is a good time to build before interest rates start to climb.”
“Warehouse space is cheap.”
"...the budget is already approved.”
They all reminded me of the times when I would eat all I could at a buffet even if overeating made me feel bad afterward. I felt bad and no sooner than when I was done. My perception of value was so warped that even a bad experience felt personally and without delay didn't cause me to change my habit at buffets.
Short-term (local) optimization and long-term (global) suboptimzation is the norm for decision making at companies I've worked for. It's difficult to overcome through reason (logic) alone. A transformation of perception must happen within. Very few people or companies achieve that.
Best regards,Shrikant Kalegaonkar (twitter: @shrikale, blog: https://shrikale.wordpress.com)
Add new comment