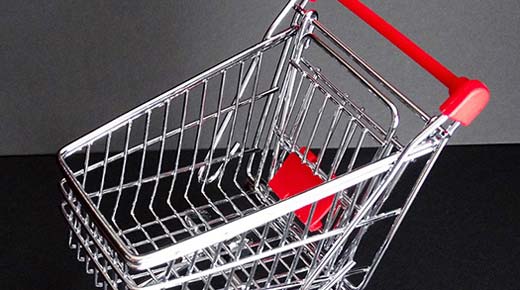
Most often when we think of a wheel, it’s in the context of transportation, one of the more obvious and ever-present of the 7 wastes in lean. In fact, the first likely use of a wheel and axle was not for transport but for processing—actual work.
ADVERTISEMENT |
According to the Smithsonian, the potter’s wheel dates to 3500 BC. The wheel and axle weren’t used for human transport (the chariot) for several hundred more years; the idea of carting material apparently took several millennia after that! The wheelbarrow was invented around 100 AD in China, and it took another thousand years more for it to appear in Europe.
From a human standpoint, these conveyance devices are designed to reduce strain. In a technical sense, it can be said they multiply our capability to do work, at least the force-times-distance kind of work: W= f x d. The problem is that although conveying material on wheels is embedded in our thinking as an improvement over manual transport, it’s actually a mechanization of waste. We may think the wheel has increased our ability to do work, but it really has increased the amount of waste we can create. Odd.
…
Comments
More productive but Less efficient
So what you're actually saying is that the wheel has made us More productive but Less efficient. In an opposite way of looking at things How many products do you know of through R&D have made the wheel obsolete? Such as the hardisk of a computer.
Add new comment