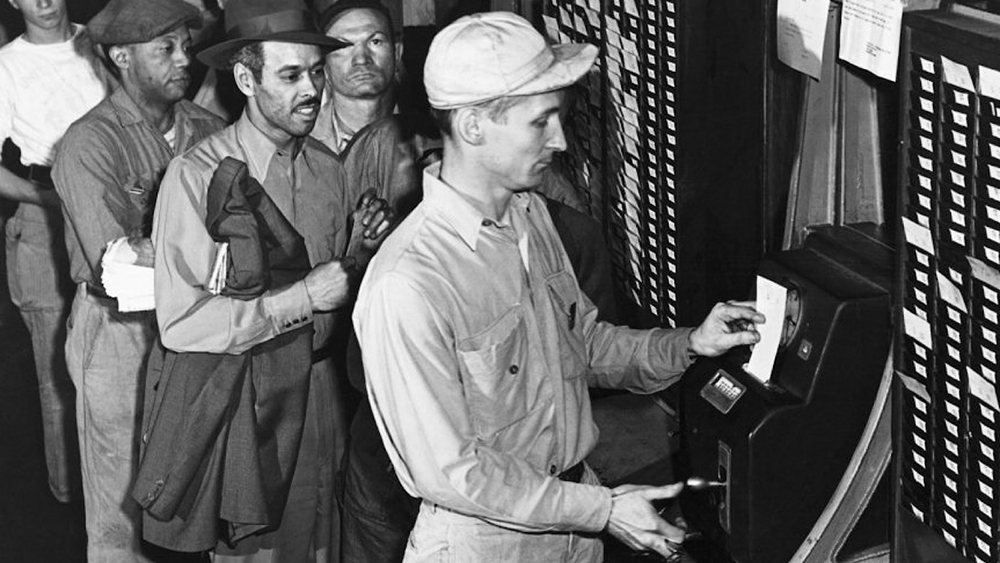
This year marks the 35th anniversary of a remarkable and unfortunately also singular event in my career: In 1985, my employer, United Electric Controls (UE), elected to remove time clocks from the factory.
ADVERTISEMENT |
At the time of this unusual decision, I had already been employed at UE for 14 years in a variety of office jobs. I worked in a building a couple blocks away from the factory, and “punching the clock” had never been a part of my day. From my first day of employment, my attendance was tracked by exception—sickness, personal time, or vacations—pretty much on the honor system. But in 1985, coincidentally around the time I transferred into manufacturing, the idea to remove the time clocks was floated. I weighed in as member of the management team on this idea, but I was pretty much a bystander, a new kid on the block, still unaware of significance of the change.
…
Comments
Time Clocks
At one time, I worked for a company (name withheld to protect the guilty, the innocent, and the naive) which used, and probably still does use, time clocks. A beautiful system, employees punching in and out (with lines), clerks scurrying around to collect, tablulate, record hours, and return cards. Unfortunately, the clocks were maintained by maintenance workers who also punched in and out. By judicious inflating of parts orders, they had soon built their own time clock and could replicate any scenarion of clock in/clock outs. No one could truly ascertain how long this activity had gone on before being exposed by a fluke coincidence. I should note at this point that, had there been no time clocks, the coincidence would have still revealed the cheating.
The cards are being replaced by computerized systems but, human nature being what it is, there are those who will attempt to hack the system just for the fun of it, and some small percntage that will take advantage of it.
Add new comment