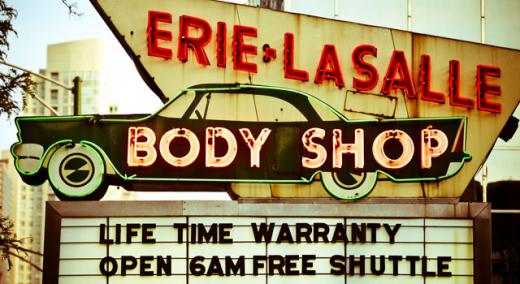
"Life Time Warranty, Plate 2" Credit: Thomas Hawk
This article contends that we should replace “quality” with “value” to address an enormous array of previously unaddressed risks and opportunities. Poor quality is only one of the Toyota Production System’s seven wastes, and it is rarely the most costly one because it is also the only waste to draw attention followed by corrective and preventive action. The other wastes can hide in plain view for literally hundreds of years (as proven by brick laying) and are present 100 percent of the time as they are built into the job. Even the Toyota Production System’s seven wastes do not encompass all potential wastes.
ADVERTISEMENT |
It might even be instructive to say “value management” instead of “quality management,” and “value engineering” instead of “quality engineering.” The U.S. General Services Administration already defines value engineering as “... achieving essential functions at the lowest life cycle cost consistent with required performance, quality, reliability, and safety.” Investopedia defines value as the “ratio of function to cost.” This article will define it as the ratio of utility (i.e., what we can do with the product or service) to its overall cost.
Value = Utility/Cost
…
Comments
Value and David Garvin
Thanks for the column William. I was hoping to see David Garvin's Eight Dimensions of Quality, published in Harvard Business Review in 1987. The column mentioned three of them. Here is the link to the HBR article: Competing on the Eight Dimensions of Quality (hbr.org) When we published The Improvement Guide in 1996, we had added six more, all 14 Dimensions are listed in the table below. We also defined the Value = Quality (Operational definitions of the 14)/ Total Cost (Price tag + cost to use). Total Cost leveraged Deming's Point #4, Stop buying on price tag alone.
1.
Performance
Primary operating characteristics
2.
Features
Secondary operating characteristics, added touches not included in other dimensions
3.
Time
Time waiting, cycle time, product available in market window
4.
Reliability
Extent of failure-free operation over time
5.
Durability
Amount of use before replacement is preferable to repair
6.
Uniformity
Low variation among repeated outcomes of a process
7.
Consistency
Match with documentation, forecasts or standards
8.
Serviceability
Resolution of problems and complaints; Service Recovery
9.
Aesthetics
Relating to the senses such as color, fragrance, fit or finish
10.
Personal Interface
Punctuality, courtesy and professionalism
11.
Flexibility
Willingness to adapt, customize or accommodate change
12.
Harmlessness
Relating to safety, health or the environment
13.
Perceived Quality
Inferences about other dimensions; reputation
14.
Usability
Relating to logical and natural use; ergonomics
Excellent reference
The HBR article you cited is worth reading. This is something I did not know until I read it: "In 1950, only one-third of the U.S. Navy’s electronic devices worked properly. A subsequent study by the Rand Corporation estimated that every vacuum tube the military used had to be backed by nine others in warehouses or on order."
The eight dimensions cited seem to relate primarily to utility (the numerator of the value equation) noting that something that lacks performance, reliability, serviceability, durability, conformance, and so on is of limited utility even if it is given away for free. These are nonetheless important aspects of the needs and expectations of customers.
Add new comment