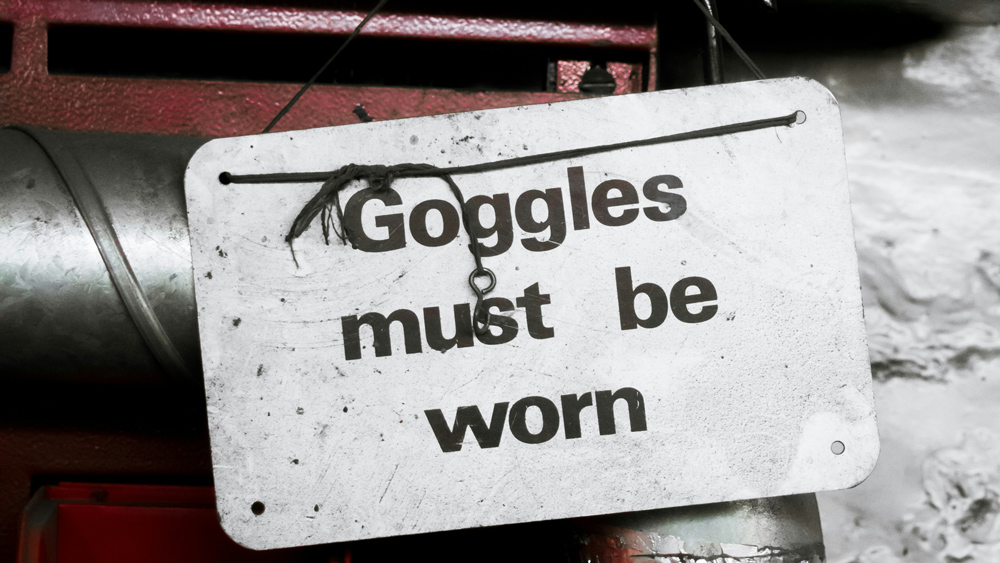
Sure, the message is clear. But does your signage have the right tone? Photo by Adam Birkett on Unsplash
In the world of continuous improvement and lean management, clear and respectful communication is crucial.
ADVERTISEMENT |
Let’s take a moment to examine two different approaches to communicating a simple instruction regarding the operation of a centrifuge, as seen in the images below—pictures I took in a hospital laboratory where I was working 15 years ago or so.
On the left (below), we have a handwritten sign that I discovered one day that reads, “DO NOT CHANGE SPIN TIME. Should be 6 Min.” It’s a direct command that leaves little room for understanding or buy-in from the team. While the intent is clear, the tone can be perceived as authoritarian and dismissive, which might not resonate well with employees. This approach assumes that the instruction is enough without providing context or reasons.
…
Comments
Are you kidding me? Should…
Are you kidding me? Should we change stop signs to pink? What a ridiculous article! Why don't we just eliminate signs and let people decide what they want to do so we aren't being "authoritative" at all? Please, write about subjects that matter.
This is a good approach
This looks consistent with the job breakdown sheet, where the reason for each step of the job is provided.
For example, "Goggles must be worn" should be accompanied by the description of whatever hazard is present because it might not be obvious.
Add new comment