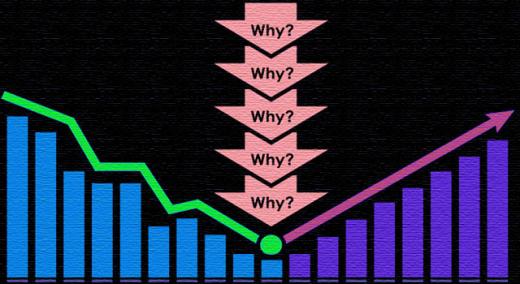
If you are wondering whether your organization could benefit from formal root cause analysis (RCA) and corrective action training, read on to see if any of these issues are present in your day-to-day operations. RCA and corrective actions are some of the most useful tools for continual improvement.
ADVERTISEMENT |
Here’s why you should include them among your company’s (and all employees’) tool set.
1. High number of NCRs in your company
It’s true that the number of nonconformance reports (NCRs) will depend on the volume of operations a specific company has. Therefore, the “number” of NCRs is a relative figure. However, if you know you have a high number of NCRs, the issue may be that you are not performing effective RCA and corrective action.
…
Comments
This article addresses the biggest source of audit findings.
BSI (2019) cited clause 10.2.1 as the greatest source of major IATF 16949 findings, and IATF 16949 clause 10.2.3 (problem solving) as the second greatest source; 10.2.3 is related directly to CAPA. These add up to about 34% (1/3) of the major nonconformances. (Brown, Robert. 2019. "Beyond the IATF Transition: Analysis of Non-Conformities and Next Steps" (BSI webinar, January 22 2019)).
My own position is that, because so many other processes of the quality management system (ranging from customer complaints and audit findings to outputs of the management review meeting) depends on CAPA, inadequate CAPA and root cause analysis could well be the biggest source of findings across the board. This makes this article on root cause analysis and CAPA training particularly worth reading.
I would even take it a step further by adding that CAPA can be used on all seven Toyota production system wastes and not just poor quality, if we treat a gap between the current state and a desirable or possible future state as a "nonconformance." This could be a gap as identified in an energy review (ISO 50001).
AIAG's Effective Problem Solving (CQI-20) cites three root causes. The traditional occurrence root cause is why the problem happened. The escape root cause is why it reached the next process (if it did), and the systemic root cause is why the planning process failed to prevent it. This ties in with FMEA where the prevention controls seek to disable the occurrence root cause of the failure mode, while the detection controls seek to intercept any poor quality that is created before it can reach the next process.
As you point out, "If corrective actions span from similar sources or mistakes, there is a very good chance they are not being addressed appropriately to begin with." This could mean that corrective action taken in one part of the organization is not deployed to similar activities elsewhere (read across/replicate process); Henry Ford once wrote that the benefit of our experience cannot be thrown away.
Add new comment