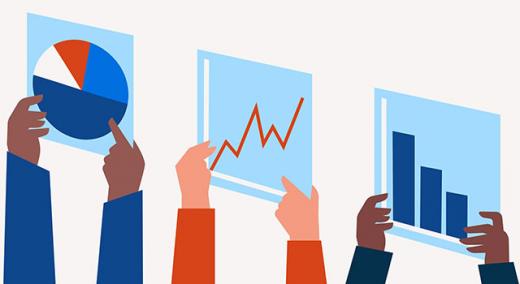
Corrective and preventive action (CAPA) is a core function in any quality management system (QMS), and a critical piece in the plan-do-check-act process approach. Like any quality process, tracking CAPA key performance indicators (KPIs) is crucial to continuous improvement.
ADVERTISEMENT |
It’s also a focus of regulators and auditors, and is consistently highlighted in the more than 500 warning letters issued to date in 2022 by the U.S. Food and Drug Administration (FDA).
Many companies take a reactive approach to corrective actions. Unfortunately, reacting to issues that get the most attention isn’t an efficient way to manage quality issues. Rather, tracking CAPA KPIs is a proactive strategy that helps prioritize issues and improve root cause analysis as part of best practices driving quality improvement.
Let’s look at eight CAPA KPIs that can help manufacturers achieve these goals, plus best practices for setting targets.
…
Comments
Too Many
Eight KPI's just for CAPA's? We only track nine KPI's for the entire 100-person company. In my opinion this is way too much beauracracy.
Valuable information
This article provides some very valuable information, as inadequate CAPA is a major source of ISO 9001 and IATF 16949 findings. This is not a surprise because so many other processes of the quality management system depend on CAPA. E.g. 8Ds (Eight Disciplines) that never get past D3 or D4 mean the the problems never get fixed and continue to make trouble. These KPIs are well worth reading, and I encourage readers to see if they have noticed any of these issues in their own CAPA process.
8 CAPA KPIs
ISO 9001:2015 nor ISO 14001 nor ISO 45001 say "CAPA". They ONLY have CA. Reason, risks based thinking is embedded throughout these ISO/IEC Directives Annex SL 9 Harmonized Structure 'clauses'.
Secondly, "risks and opportunities" planned actions are required for CONFORMANCE not 'compliance', is required to be "integrated within the organisation's business processes".
CA and PA in medical, automotive, aerospace, food, medical products, oil & gas are some QMS Standards that ADD 'PA' to their QMS requirements. These MS standards have either referenced or included ISO 9001:2015 requirements.
CA and PA must be separated. They are very different and any 'Continual Improvement' (not "Continuous Improvement") methodology like 8D, PDCA, DMAIC, A3, PDSA et al can be used as per the ISO 9001:2015 "Context of the organization". Correctly, PA by say FMEA et al, are most valuable.
Worth re-reading ISO 9000:2015 Vocabulary and terminology as it a "Normative reference" for ISO 9001:2015 and hence embedded within ISO 22000 etc, for explaining CA and PA. Notice - not "CAPA". ISO 31000:2018 Risk Management - Guidelines and directly, ISO 31010:2019 provides a drill deep and wide RM assessment and mitigation tools and techniques.
Add new comment