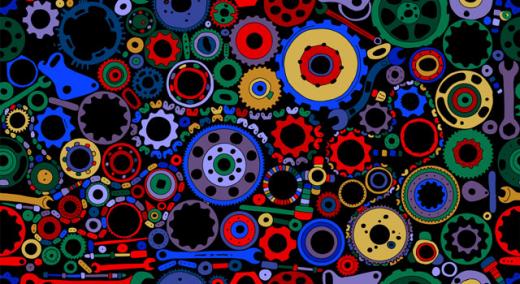
During the last several decades, the ability to manufacture customized products for customers has become increasingly attractive to a growing number of companies. However, customization has led to manufacturers drowning in a sea of increasingly complex bills of material (BOM).
ADVERTISEMENT |
Standard products are great when product changes are minimal, when identical products can be put into identical boxes hour after hour. The custom world, on the other hand, is always dynamic and ever-changing. Common tools that work well for standard design, engineering, and manufacturing resist adaptation into solutions for customization. An early symptom of looming problems is the need for huge repositories of parts masters or BOMs to be maintained.
Issues with the ‘150-percent BOM syndrome’
There are solutions that draw from established technologies and are designed from the ground up for dynamic, generative methodologies. Before outlining these, we must dig deeper into why standard solutions cause problems.
The drive to somehow repurpose standard practices into a custom infrastructure has led to the well-known “150-percent BOM,” also known as “master BOM,” “variant structure,” and “configurable BOM.”
…
Add new comment