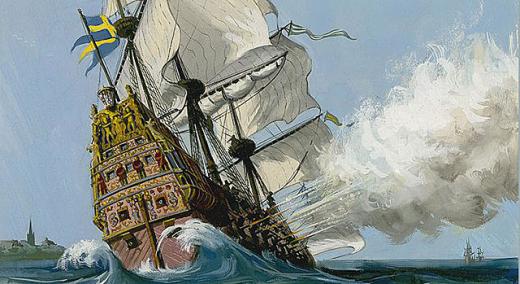
What is the Vasa? It was a Swedish warship built in 1628. It was supposed to be the grandest, largest, and most powerful warship of its time. King Gustavus Adolphus himself took a keen personal interest and insisted on an entire extra deck above the waterline to add to the majesty and comfort of the ship, and to make room for the 64 guns he wanted it to carry.
ADVERTISEMENT |
This innovation went beyond the shipbuilder knowledge of the time... and would make it unstable. No one dared tell him. On its maiden voyage, the Vasa sailed less than a mile and sank to the bottom of Stockholm harbor in full view of a horrified public, assembled to see off its navy’s—and Europe’s—most ambitious warship to date.
What reminded me of the Vasa? The time has been ripe for visible motivational speakers to weigh in on Covid-19 and “inspire the troops.” From a speech using the Vasa as a backdrop:
…
Comments
Healthcare Has Been Admiring the Problem
At IHI in 2006, Dr. Berwick asked attendees to "Pledge allegiance to science and evidence," by which he meant control charts, histograms, Pareto charts and other quality tools.
Ten years later, in 2016 in his closing keynote, Dr. Berwick again emplored attendees to "Pledge allegiance to science and evidence." His tone of voice told us he was not happy with the progress made.
Many key indicators, such as patient harm, have not changed in the last decade. The IHI estimates that one in every two patients suffers some sort of preventable harm.
Hospitals have a window of opportunity during the summer lull to implement changes to make healthcare faster, better and cheaper with better patient outcomes and less patient harm.
The IHI also estimates that healthcare wastes a Trillion dollars every year. They announced a goal to cut waste by 50% ($500B/year) by 2025. This will require dedication and focused improvement across every aspect of healthcare delivery.
Will this pandemic usher in an age of transformation? Only time will tell.
I'm not happy either!
Just like Berwick was "tired of excuses" in 1997. Sigh...
It's become a tired, predictable, patronizing, scolding parent "schtick" (always complete with a sound bite)...and a very profitable one. He should look in the mirror and give himself a scolding. Why hasn't he taken personal accountability for the disappointing lack of results caused by his, for lack of a better term, "improvement malpractice"? I'm tired of his public statements of how tired he is of excuses...meanwhile "crying all the way to the bank."
Given his fame and influential contacts, why hasn't he been held accountable for his role in silently tolerating executive behaviors propogating longheld barriers and cultural handcuffs? In my article, look at the link to his 1993 speech -- things he wanted solved IN TWO YEARS...that continue today (maybe token progress on two).
I am shocked...SHOCKED! (not really)
[Standing ovation]
Who's against this? I can just see Deming's dreaded glare and growl: "A goal without a method is nonsense! BY WHAT METHOD?" Juran even said, "There is no such thing as 'improvement in general'."
Starting with IHI's 100K lives campaign (December 2004), "politics" crept into improvement, and it's since become an ongoing tired game of justification via a series of vague solutions to vague problems yielding vague results. Method? -- "Vasa du jour," churning out "qualicrats" by the thousands imposing improvement KoolAid on people who, God bless them, think working HARD and doing their best is "quality."
Deming said, "If everyone did their best, 95 percent of problems would remain." He also said, "It is not enough to do your best; you must know what to do and then do your best."
Put focused attention on ANYthing and it will improve. And "stopped clocks" always tell the right time twice a day -- as Bob Emiliani says (from his 7 laws of lean disillusionment): "Results that live up to expectations are an accident." There will always seem to be just enough vague results to justify calling it "successful." And then out comes a Ouija board to massage the "vague data" and allegedly prove it (like the 100K lives...). Then it's...
..."NEXT!"
You are right: they do admire how much they admire the problem.
I always appreciate your comments, Jay.
Another excellent article!
Hey, Davis,
Last year I was thrilled (at first) to get involved with a major hospital system's initiative to become a Highly Reliable Organization (HRO). One of the five principles of HRO is "reluctance to simplify." What this means is that you have fo consider the whole cause system when studying a problem, and essentially use good science to drive past the surface symptoms to the actual causes of the issue. Of course, the doctor who was running the whole initiative decided almost immediately that they could get there using "Lean 9-block A3" projects, and said that statistics just "never caught on" in that organization, so he didn't want anyone getting confused. A few weeks later, he decided that "reluctance to simplify" was too hard to explain and too hard to remember, so he changed it to "get to the root causes." I never did get to ask him if he saw the irony in simplifying "reluctance to simplify."
So, not much hope there...
Always good to hear from you
Thanks for the kind feedback, Rip, and for sharing another frustrating story that once again proves we could never even begin to make up the things we encounter.
To adapt the amusing quip attributed to either Sam Goldwyn or former President Gerald Ford, "If Dr. Deming were alive today, he'd be spinning in his grave."
Improvement continues in its thriving "Vasa du jour" efforts...and ongoing avoidance of the needed rudder of data sanity.
The Solution Is Not That Complex
Most IHI improvement posters use Line and Bar charts with useless trendlines--the dumb and dumber of charts.
I have suggested that if the IHI wants control charts, Pareto charts, Histograms, fishbones and the other tools of quality that they should require them in all improvement posters. No tools? No proof? No poster.
Can you and I just stop pretending to keep being surprised?
Jay, what you describe is a perfect example of another of Emiliani's other Laws of Lean Disillusionment:
If they did what you suggest, the poster room would be pretty empty...and "the customer" wouldn't like it one bit!
Add new comment