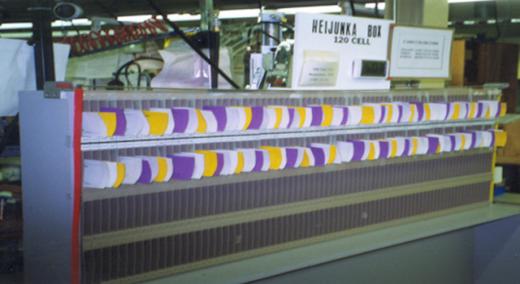
There’s a certain irony in the recent attention paid to the application of robots on the shop floor. On a couple occasions in the past year, I’ve heard manufacturing colleagues talk about the benefits of deploying robots to handle material conveyance. “Better,” they say, “to redeploy humans to value-adding jobs where human capability and creativity can benefit the customer.”
ADVERTISEMENT |
Given the persistent labor shortage, I get the benefit of filling open job slots. What’s confounding to me is the tendency to ascribe terms like value-adding and non-value-adding (NVA) to specific jobs rather than applying such terminology to wasteful activities within the jobs.
…
Comments
Article
Good use of humor for an often neglected situation
Add new comment