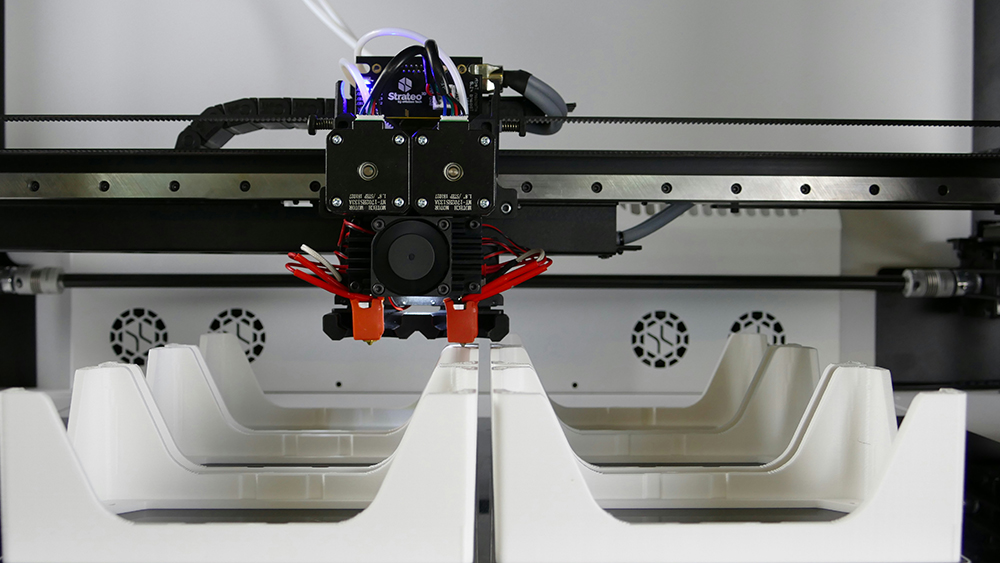
Industry is increasingly looking to additive manufacturing as a path to restore domestic capacity for fabricating large metal structures, much of which has moved overseas. Photo by eMotion. Tech on Unsplash
Scientists at the U.S. Department of Energy’s Oak Ridge National Laboratory (ORNL) have determined how to avoid costly and potentially irreparable damage to large metallic parts fabricated through additive manufacturing (AM), also known as 3D printing, caused by residual stress in the material.
ADVERTISEMENT |
Industry is increasingly looking to AM as a path to restore domestic capacity for fabricating large metal structures, much of which has moved overseas. Rather than reestablish massive foundries in the United States, 3D printing could be used to create large parts, shortening supply chains and allowing industry to quickly acquire needed tooling and other parts. But first, research is needed to ensure 3D-printed parts can withstand the stress of the printing process.
The ORNL researchers determined through computational modeling that large-scale, additively manufactured metallic parts can develop considerable residual stress, or RS, within the material. The RS buildup results in crack formation during the hot printing process and grows larger as the material cools, infiltrating the metal and causing irreversible damage.
…
Add new comment