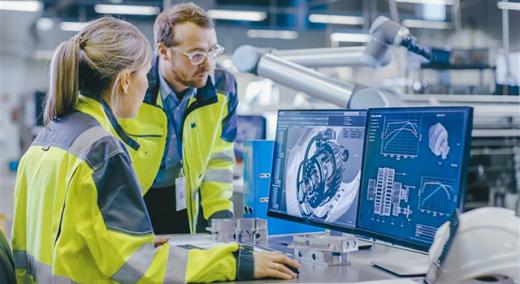
In an earlier article in this series, “Cybersecurity and Industry 4.0: What You Need to Know,” we discussed the four aspects of Industry 4.0: cyber-physical systems (CPS)/cobots, internet of things (IoT), cloud manufacturing, and automation, as well as how they are interconnected. Strong cybersecurity practices protect those interconnections, ensuring manufacturers’ systems consistently deliver accurate data in a timely manner—something critical to the success of an Industry 4.0 model.
ADVERTISEMENT |
In the past, enterprise systems in manufacturing facilities had distinct boundaries. The shop floor was separated from the office functions of the company both physically and electronically. Few production systems were connected to each other or the internet. In some ways, this approach, commonly known as “air gapping,” gave reasonable protection for small manufacturers. Without the risks associated with connectivity, manufacturers were seen by attackers as hard targets and not worth the effort.
…
Add new comment