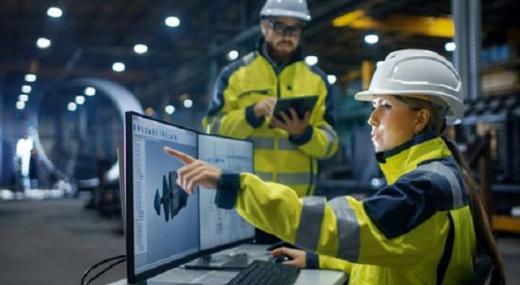
This morning my favorite local morning news program had an interesting segment on new slang words and what they mean. While the definitions were probably not necessary for millennials or generation Z, but for baby boomers like me, it was an eye-opening vocabulary lesson. I must admit I didn’t know what boujee meant, even though I had heard it a few times—like when my niece said the wine glasses I used at Thanksgiving were boujee.
ADVERTISEMENT |
Perhaps you’ve heard some phrases lately that suddenly seem like they’re everywhere, such as Industry 4.0. When I first heard the term, I wasn’t quite sure what it meant, but it seems to be one of the hottest phrases in manufacturing.
There have been four major technological trends during the past few hundred years that have revolutionized both industry and manufacturing. The first was the combination of mechanization with steam and waterpower. The second combined mass production and electricity. The third was the rise of electronic and information technology (IT) systems and automation.
…
Add new comment