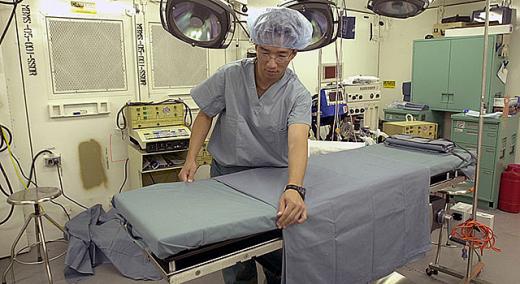
Last February I had the opportunity to observe healthcare providers up close and personal at one the world’s premier hospitals. “Who Cares for the Caregivers?” was written from the perspective of a patient in a cardiac step-down unit, sympathetically watching caregivers as they grappled with many small problems in their workday. Here is another story from the 8th-floor recovery area.
ADVERTISEMENT |
At 3 a.m., except for the sound of occasional call bells, the floor was quiet. Nurses and assistants quietly made rounds to dispense meds, check vitals, and draw blood. Patients were resting quietly when I was awakened suddenly by a bright light over my bed.
…
Comments
Small Things
Thank you so much for recommending this to the CNA (and I'm so proud of her for taking action!). I guarantee that she is probaby looking at other things that can be solved like this and taking the steps to improve the work environment and efficiency!
Add new comment