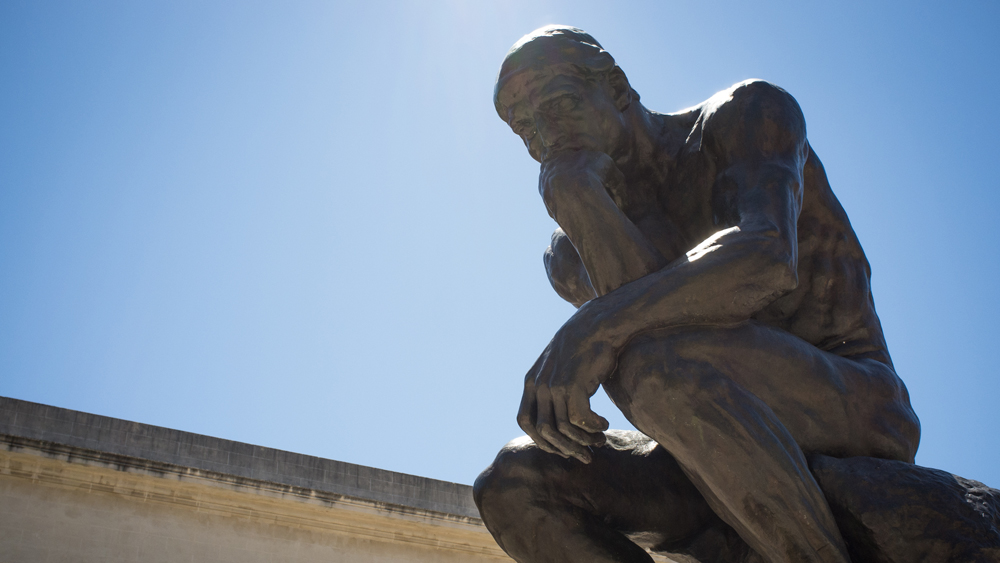
Body
I once attended a presentation that Eli Goldratt gave for the Society of Manufacturing Engineers. We were seated in an auditorium, listening as Goldratt paced back and forth on the stage, puffing on his cigar, gesturing for effect, and occasionally cursing for emphasis. The author of The Goal (North River Press, 2014 fourth edition) and creator of OPT (optimized production technology) was describing what later became known as the Theory of Constraints (TOC).
ADVERTISEMENT |
…
Want to continue?
Log in or create a FREE account.
By logging in you agree to receive communication from Quality Digest.
Privacy Policy.
Comments
Fear of Failure
People often fear failure or looking foolish when tackling problems using TOC, Lean Six Sigma, etc. In the last century, much of this was done manually leading to errors. In the 21st Century, software will automate much of the analysis. Stop worrying. Start using available software and the tools of quality to make quantum improvements.
There's a cartoon in Jack Canfield's book, Success Principles, that I like. The child asks the father what he makes at work. The father says: "What do we make at work? We make excuses."
Stop making excuses.
Start improving. Yes you may stumble, but pick yourself up, learn something and do it again. That's how we get better individually and collectively.
Add new comment