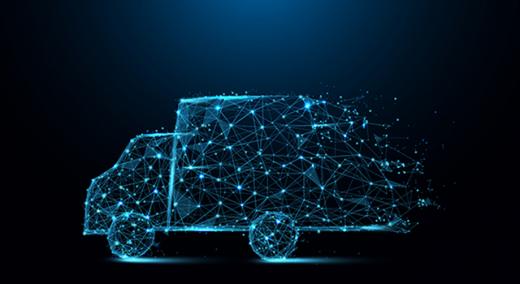
Imagine building a brand over decades. Hundreds of millions of dollars invested in design and development. Sponsorships with celebrity athletes and professional and college teams. Leading-edge marketing making your company one of the top 20 brands in the world. It only takes one incident to unravel all this investment.
ADVERTISEMENT |
Nike found that out the hard way when Duke University superstar Zion Williamson ripped through the sole of his Nike sneaker 33 seconds into the grudge match with North Carolina. Williamson ended up leaving the game with a knee sprain, Duke went on to lose the game, and millions of viewers were left wondering if Nike’s quality was up to par. The immediate reaction by investors the next day was a more than 1-percent drop in shares, equating to $1.1 billion in market value. Ouch... on so many levels. It’s a reminder of how important product quality is to a company, the brand, and consumers.
…
Add new comment