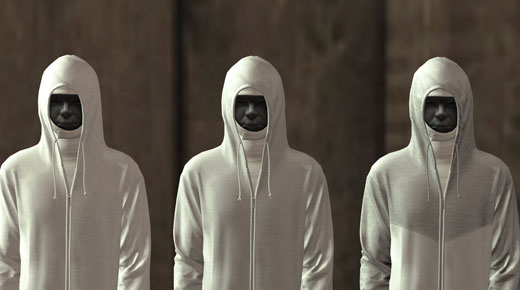
Credit: Melusina Parkin
The recent revelation that a major steel maker falsified test data,1 and similar scandals at other companies,2 underscores the menace of counterfeit parts, or what a 1987 Senate hearing called COME UPS: COunterfeit MatErials and Unauthorized Product Substitutions. The history of COME UPS shows the potentially catastrophic outcomes for which the manufacturers involved can be held civilly, and criminally if a government contract is involved, responsible.
ADVERTISEMENT |
Tsar Peter I of Russia recognized this issue almost 300 years ago when, in January 1723, he issued a decree that began by ordering a factory owner to be flogged and banished to hard labor for selling defective small arms to the Russian Army. A foreman alderman was to be flogged and banished to Azov for putting trademarks on faulty muskets, i.e., passing products he knew to be nonconforming. Peter went on to command that, if a stoppage (i.e., failure to fire) took place during combat, those responsible would be subject to punishments ranging from flogging to loss of their Sunday vodka rations.3
…
Comments
Counterfeit parts
Unfortunately, as a society, we have not seen fit to make people personally responsible for these events. In most instances, the companies involved will have made enough money on substandard products that the fines and penalties can be considered as minor issues.
Too exacerbate the problem, unscrupuous manufacturerers create a pricing structure that can force quality organizations out of business. The old saying "Bad money drives out good!" is equally applicable to product.
Add new comment