All Features
Ken Koenemann
In my first article on relevant metrics and key performance indicators (KPIs), I explained why limiting management’s strategic planning to high-level goal setting is doomed to failure. For strategic goals to be realized, they have to be translated into daily KPIs that are meaningful to everyone in…
Ken Koenemann
During annual strategic planning meetings, the temptation is always to spend most of the time working on the business, discussing the big-picture strategic plans and breakthrough developments that are critical to the future of the company. But just looking at long-term plans ignores a critical…
Laurel Thoennes @ QD
“What makes a personal kanban any better than a to-do list?” asked Julie, crossing out a completed task on her “ta da!” list with exaggerated strokes.
“With personal kanban you visualize your work, it becomes tangible, you get kinesthetic feedback, it’s flexible, contextual, and it promotes…
Pete Abilla
Some time ago, while consulting for a huge call center, I took a group of customer service agents for a little gemba walk and a quick activity to demonstrate a few lean fundamentals. What was scheduled for a 60-minute exercise turned out to be an experience that awakened the agents, several of whom…
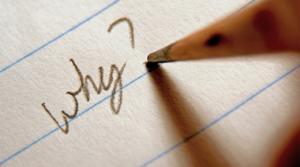
Stewart Anderson
The 5 Whys is a well-known root cause analysis technique that originated at Toyota and has been adopted by many other organizations that have implemented lean manufacturing principles. Unlike more sophisticated problem-solving techniques, the 5 Whys doesn’t involve data segmentation, hypothesis…
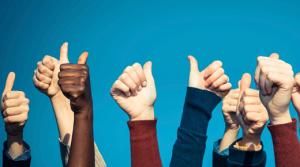
Craig Cochran
Training is profoundly strategic. It’s a process aimed at improving the single most important resource in the organization: people. Nothing affects customer loyalty more than the behaviors and competencies of employees.
Training is the most effective way to communicate the correct behaviors and…