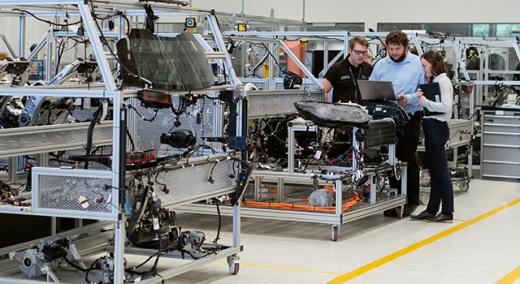
Credit: ThisisEngineering RAEng on Unsplash
A root cause analysis (RCA) should be empirical; however, this can be difficult when dealing with human error. A typical human failure is a missed operation, such as when a process step isn’t carried out. This could mean a part wasn’t installed, a bolt wasn’t tightened, or a server didn’t deliver a food item that had been ordered.
ADVERTISEMENT |
The simplest answer in such a situation is “the employee forgot.” Perhaps, but there’s often more to the situation than simple forgetting—and forgetting isn’t so easy to evaluate empirically. We can’t ask somebody who assembles hundreds of parts a day, “Did you forget to tighten a bolt four months ago?” We have only the evidence, in the form of an untightened bolt, and the untestable hypothesis, “employee forgot.” Fixating on the untestable hypothesis does little to identify the cause of the problem so that adequate corrective actions can be implemented. This is the point in supplier quality where the supplier often submits an 8D report listing both the root cause, “employee forgot,” and the corrective action, “employee retrained.” Such actions do little to prevent a reoccurrence of the failure.
…
Comments
Errors in Empirical RCA
G'day Matthew,
Thought the Subject would get a response.
In your story, there is much said about 'process' and where the person could have made an error. And yes, how many times do we see one cause being the Person (not 'Man' anymore); worse in Process Control / Reaction Plans is the 'solution' to be "retrain the operator". Yes, I agree it still happens.
If I may - Dr Ishikawa had 3 types of "Cause Analysis" (See Guide to QC book). Your process is correct and hence Ishikawa's "Process Classification Cause Analysis" is most relevant and - correct. Don Dewar (RIP, ex-QCI International President) called them Process Cause and Effect). The Type A and B are okay for Event problems / effects, but not for causes in a process.
All Ishikawa “Cause Analysis” activities are to clearly define the problem and for causes, data to be collected (empirical – variable and attribute), then graphically summarised and analysed for causes or symptoms, then solutions to the cause and hopefully ‘root cause’. As in Industrial Engineering, Work Study guidance in the Flow Process Chart, ‘Why’ is asked against that Root Cause for What, When, Where, Who and How.
The "Causes" shown too would be in Dr Ishikawa's view, too generic also “TAKT Time, Part Missing, Documentation” et al. The Schematic says, "Poke Yoke" and in the text says "Poka Yoke" - human or publisher 'error or a Six Sigma DPMO?
Being such, it makes it difficult as you said, to collect and verify each cause unless evidence, data and graphical analysis can then provide your "Empirical Analysis".
Yes, Dr Deming did say “85:15” and was first mentioned in his 1978 Tokyo JUSE and IAQ Conference. He, Drs Ishikawa and Juran et al presented. Deming adapted what Dr JM Juran called his “80:20 / Pareto Rule” in 1948.
Interesting when I was with Dr Juran in Australia on one of his many visits, as did Dr Deming, that Juran said he and Deming realised that perhaps, given what they then and seems to be nowadays, to be still the case, the 80:20 or 85:15 should be 95:5 ratio.
I agree with a great extent
I agree with a great extent to your point, Ishikawa diagram has though to be a final building-stone in the problem solving models, however the diagram is more likely addressing process (or System) environment than digging into back-causes.I work in a Japanese company with a Japanese people who have been practicing tons of problem-solving models and root-cause analysis schemes, their systematic and structural behaviour is largely based on using 5-whys for analysing causes that popped up from Ishikawa diagram.
Moreover, addressing human causes require alot of deep understanding of the process and organization culture. I have witnessed some positive results with such acitivities.
Regards,
Moataz
Empirical RCA
Great to read '5-why analysis' on the causes of the problem / the effect as per Toyota Practical Problem Solving Methodology and earlier through Dr K Ishikawa. Sadlly some folk mistakingly gone straight into '5-Why' on the problem. Interesting too Dr Ishikawa never called his Type A and B (Event Cause Analysis Diagrams) a "Fishbone".
Human Error and RCA
Generally, I would use an Ishikawa diagram to list hypotheses. Then, I would prioritize and investigate. Once a cause has been found and confirmed, I agree fully with using five whys. However, I find five whys is often used to brainstorm potential causes to solve. That makes sense if the objective is quality improvement through the elimination of potential failures. For finding an actual cause, every why question must be investigate to find the answer. I lean towards expanding branches as I dig deeper, although a I do not object to starting a new Ishikawa diagram.
In the example above, the cause of a product failing is known. An operation was missed. The cause of a human error may be impossible to confirm, such as one operation that was skipped in one assembly out of hundred produced months before. In such a case, I would use the Ishikawa diagram above and aim for improvement though the elimination of potential failures.
Add new comment