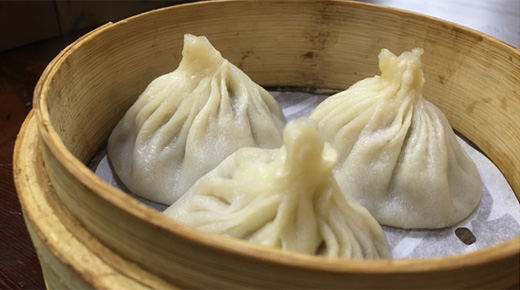
I have been writing about kaizen a lot recently. It is a simple idea: change for the better. Generally, kaizen stands for small incremental improvements. Here I’m going to look at what is the best kind of kaizen.
ADVERTISEMENT |
The twist in the dumpling
A few posts back, I talked about the order for kaizen, including the idea of equipment kaizen or setsubi kaizen. To introduce the concept of the best kind of kaizen I will share a story from Masayasu Tanaka, dealing with equipment kaizen. He tells of a plant that manufactured steamed dumplings (manju in Japanese). They were trying to automate the entire process of making steamed dumplings, a directive that had come directly from the president of the company.
The last step of the process was to make a twist on the top of the dumpling. All the previous steps were easily automated; however, the twisting of the top stumped them. Finally, company engineers were successful in creating a machine that could indeed twist the top of the dumpling. Everybody was happy, and they cheered the smart engineers for their hard work.
…
Comments
Kaizen why it fails in Western Culture
I never understood Kaizen until it was explained by our Japanese management. The purpose is not simply continual improvement as many so-called experts sell. Kaizen is rather a continually improved pathway at every operation of an organization, toward meeting the requirements and expectations of its customers.
Kaizen is not something management can implement, rather it’s the release of responsibility and authority from management to the worker which provides the worker the autonomy to change their work as necessary so the organization can continually meet the requirements/expectations of its customers. Most Western management refuses to release that responsibility and authority and therefore kaizen will forever remain a buzz word to them.
Perhaps the most amusing point of Western management is that they assume themselves (managers and supervisors alike) to be able to control every step of every process every second of the day. This is simply nonsense. However, it’s the standard to which they hold themselves, and it’s one of the reasons why Kaizen does not work in such Western culture. The other Western management failure is to have its various departments or functions or teams, working on objectives which are averse to other departments or functions or teams within the organization. Kaizen cannot flourish in an environment such as this as it will become counterproductive, the kaizen itself not considering how it affects the whole.
Further don’t ever count the number of kaizens as prize, as that approach can be discouraging to others who have equally effective improvement ideas but either less in volume or they work within a more robust and effective process in the first place. Any reward for kaizen should be private and not public. Acknowledging kaizen and its contribution to improve the organization is sufficient
Without knowledge of the product or service being provided and the requirements and expectations of the customers, and without the responsibility and authority to effectively change their work processes, employees shall always fail at achieving kaizen.
Add new comment