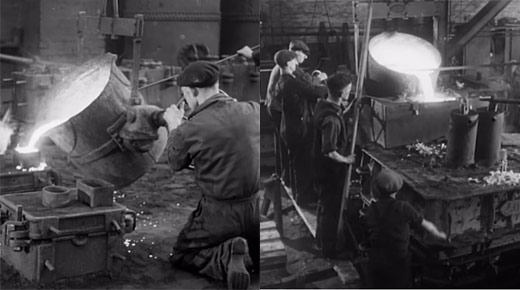
A couple of weeks ago I posed the question, “Are you overproducing improvements?” and compared a typical improvement “blitz” with a large monument machine that produces in large batches.
ADVERTISEMENT |
I’d like to dive a little deeper into some of the paradoxes and implications of 1:1 flow of anything, improvements included.
What is overproduction, really?
In the classic seven wastes context, overproduction is making something faster than your customer needs it. In practical terms, this means that the cycle time of the producing process is faster than the cycle time of the consuming process, and the producing process keeps making output after a queue has built up above a predetermined “stop point.”
If the cycle times are matched, then as an item is completed by the upstream process, it is consumed by the downstream process.
If the upstream process is cycling faster, then there must be an accumulation of work in progress (WIP) in the middle, and that accumulation must be dealt with. Further, those accumulated items are not yet verified as fit for use by the downstream process that uses them.
…
Comments
Sound strategy
As with all things, Murphy's Law is operative! Field Marshall Helmuth Karl Bernhard Graf von Moltke, Chief of the Prussian General Staff, defined this concept quite well in his "On Strategy"....
“The material and moral consequences of every major battle are so far reaching that they usually bring about a completely altered situation, a new basis for the adoption of new measures. One cannot be at all sure that any operational plan will survive the first encounter with the main body of the enemy. Only a layman could suppose that the development of a campaign represents the strict application of a prior concept that has been worked out in every detail and followed through to the very end.
Certainly the commander in chief will keep his great objective continuously in mind, undisturbed by the vicissitudes of events. But the path on which he hopes to reach it can never be firmly established in advance. Throughout the campaign he must make a series of decisions on the basis of situations that cannot be foreseen. The successive acts of war are thus not premeditated designs, but on the contrary are spontaneous acts guided by military measures. Everything depends on penetrating the uncertainty of veiled situations to evaluate the facts, to clarify the unknown, to make decisions rapidly, and then carry them out with strength and consistency.”
Add new comment