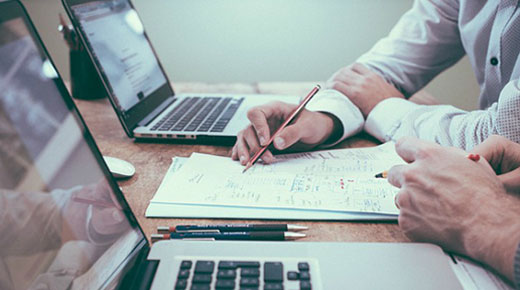
What sets the top 20 percent of innovation leaders apart from their competitors? According to LNS Research, one key difference is that a majority (52%) of the top tier has real-time visibility into manufacturing quality metrics, compared to just 9 percent of the competition.
ADVERTISEMENT |
Organizations collect quality data in a variety of ways, including audits. For companies struggling with quality problems, audits can stand in the way of identifying and fixing the underlying causes.
How is this possible when audits are meant to shine a light on your processes? Common barriers include reactive auditing methods, infrequent audits, and data integrity issues.
1. Reactive audit approaches
Improvement requires preventing problems that are likely to happen in the future. That means going beyond rear-facing product inspections to identify the process errors that cause them.
…
Comments
Useful Guidance
I enjoyed reading the piece, Paul. I found it informative. It is useful guidance for conducting meaningful audits. Just a few points for your consideration:
"What sets the top 20 percent of innovation leaders apart from their competitors?"
-- Do these companies stand outside of the distribution or are they top 20% of the distribution? If the companies belong to the distribution, that they are in the top 20% of it is due to random chance.
"...a majority (52%) of the top tier has real-time visibility into manufacturing quality metrics..."
-- So, slightly less than half of the top tier companies do not have real-time visibility into manufacturing quality metrics, yet they are in the top tier. This isn't compelling is it?
-- What proportion of companies that have visibility into manufacturing quality metrics are in the top tier? What proportion of companies that do not have this visibility are in the top tier? A comparison of these proportion may be more meaningful.
"1. Reactive audit approaches...identify the process errors that cause [the problems]"
-- Problems are not always the result of errors in the process. A properly functioning process, albeit one that is not capable of meeting requirements, can generate failures.
"3. Low audit-completion rates...Many companies with manual, paper-based systems struggle with low audit completion rates."
-- Is this a correlation or causation?
Add new comment