Content by John Niggl
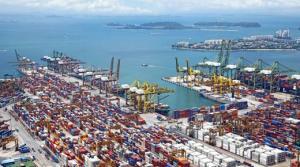
Tue, 08/08/2017 - 12:03
Ever wondered why quality control (QC) professionals check a sample instead of 100 percent of a shipment during inspection? Or maybe you’ve wondered why they use acceptance sampling, rather than simply inspecting an arbitrary quantity of goods,… A Textbook Case of Supply Chain Mismanagement How an ISO 9001 audit could have prevented the Tianjin warehouse explosions
Wed, 09/23/2015 - 16:39
On the morning of Thursday, Aug. 13, 2015, I woke to find dozens of posts from netizens clamoring about events that had occurred late the night before. There had been two massive explosions reported from a warehouse in Tianjin, a prominent port… Does the California Transparency in Supply Chains Act Affect You?Proper investigation and transparency helps ensure compliance
Wed, 07/22/2015 - 11:27
If you’re like most savvy manufacturers, you know to watch out for changes in labor laws that could affect you in countries where you have factories or where you sell your products. We’ve all seen examples of how manufacturers were held accountable… Six Ways to Maintain Quality Chinese ManufacturersAuditing, testing, and continuous improvement are worth their weight in finished goods
Wed, 03/18/2015 - 11:17
What are the best ways for a foreign company to monitor quality at a contract Chinese manufacturer? What groundwork should you lay before working with a Chinese supplier?
It should come as no surprise that China remains a major manufacturing hub…