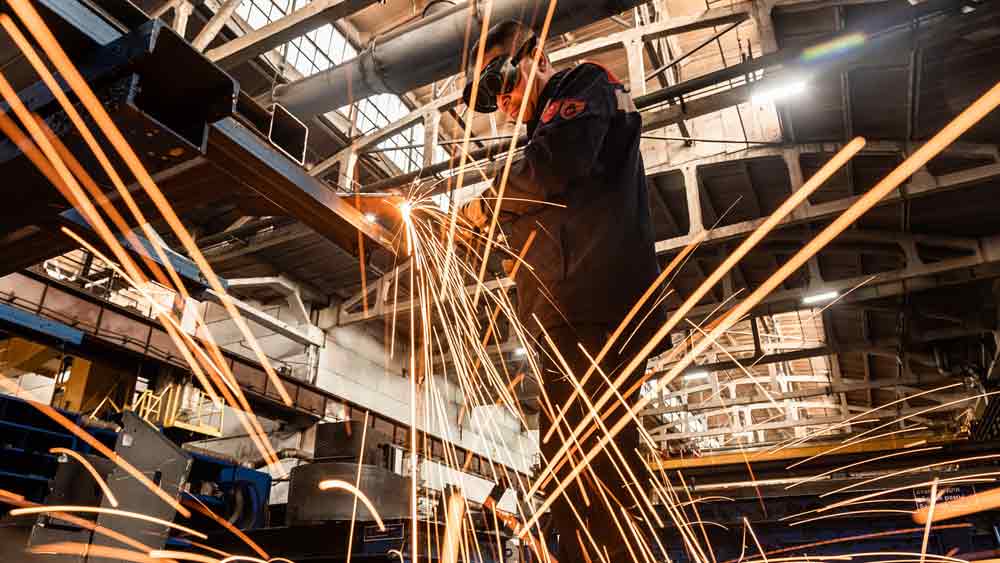
Global Shop Solutions
These are new times for manufacturers. Global pandemics. Worldwide supply-chain disruptions. Steep price increases for parts and materials. Increasingly competitive global markets.
ADVERTISEMENT |
Manufacturers are can-do people, but doing becomes harder in today’s “do more with less” manufacturing environment. Just like the lean manufacturing phase during the 1990s, manufacturers are seeking ways to simplify processes, cut costs, and get more done with fewer people.
Fortunately, the tools and technologies required to accomplish these goals are already here: automation, integration, and tailored ERP. These three tools are constantly expanding capabilities, including the ability to connect with the internet of things (IoT). Manufacturers that get to the top of the “do more with less” mountain ahead of others will find themselves with a powerful competitive advantage.
Automation
For years, automation was considered the future of manufacturing. In case you haven’t been paying attention, that future is here now, and it’s the driving force behind doing more with less.
Manufacturing automation comes from three main sources: auto features built into your ERP system, innovative computer-guided production machines, and third-party software programs that integrate with your ERP. Each in their own way helps to reduce labor costs, eliminate paper and waste, process orders faster, reduce setup and production times, and get your product out the door on time every time—all of which can be accomplished with fewer employees and with less overhead.
ERP already provides many types of automation, such as auto scheduling and purchasing. It wasn’t too long ago that scheduling required a team of planners, reams of paper, and never-ending spreadsheets to get the job done. With ERP, you enter the job data and requested due date into the scheduling application, which automatically assesses labor and machine capacity and material availability in inventory, and fits the job into the right place on the schedule.
Want to reduce head count in the purchasing department while lowering purchasing costs? Auto purchasing lets you buy parts and raw materials for less money in a fraction of the time by automatically importing and consolidating all work order and inventory information. No more hours spent poring over handwritten purchase orders. No more researching which materials are needed for upcoming jobs, because with auto reorder, you never run out of frequently used parts and materials.
Other ERP automations:
• Accounting—ERP automates many accounting processes, making it quicker and easier to complete everything from daily accounts payables and receivables to monthly closes. For example, invoices can now automatically be scanned and mapped to your ERP system, taking your employees from entering data with keystrokes to approving and moving faster by clicking.
• Inventory—With automated inventory processes, you can track material movement, such as picking materials and lot tracking, from anywhere on the shop floor, and the transaction instantly gets recorded in inventory.
CNCs
Computer numerical control (CNC) offers a great example of how machine automation can lower production costs and increase speed without sacrificing quality. Using a programmable logic controller (PLC), automated CNCs can control an assembly line, robotic device, or other processes that require high reliability. The PLC guides the cutting process by connecting to the CNC machine and sending the job data directly to the ERP system. Depending on the CNC and the complexity of the part being made, manufacturers can make parts without a human operator present, or with minimal human interaction.
CNC milling. Credit: Global Shop Solutions
Growing numbers of manufacturers are using automated CNCs for “lights out” manufacturing—making parts overnight in a dark factory without any machinists to clock in and out of the job. Making parts with minimal staff for second and third shifts mitigates the shortage of skilled employees, increases output, and reduces labor costs.
Every automation should have a clearly defined purpose and an outcome that supports your long-term business goals.
On routine or less complex processes, automated machines reduce scrap and rework by producing repeatable accuracy unmatched by highly skilled operators. Some automated machines can also perform multiple operations, eliminating the time required to move materials from one work center to another.
One caution with automation: It should be implemented carefully and with a strategic perspective that aligns with your business and operations strategies. Every automation should have a clearly defined purpose and an outcome that supports your long-term business goals.
Few innovations have affected the manufacturing industry as much as ERP’s ability to communicate with third-party software applications and other IoT technologies. And rightfully so, because your ERP system is the heartbeat of your entire manufacturing enterprise and the hub of the wheel for everything you do. Integrating ERP with third-party applications vastly increases the available data by feeding it directly into your ERP system. This enables you to make real-time decisions critical to the success of your business and lets you do it with confidence because you can trust the data.
One integration no manufacturer should be without is electronic data interchange (EDI). This integration saves time and money by enabling the exchange of business data between two computers across different platforms. Purchase orders, invoices, inventory levels, shipping notices, and other customer information can be instantly downloaded into your ERP system, eliminating the need for manual data entry and ensuring accuracy. Customers and vendors can receive data from you in the same manner.
Some of the most widely used integrations throughout the industry include:
• Radio frequency identification (RFID), a multifaceted tool that improves the speed and reliability of employee logins; facilitates faster, more accurate payroll processing and tracking of job costs; provides real-time tracking of materials movement; and more.
• CAD interface, which enables the building of huge BOMs in a fraction of the time it normally takes—a must-have if you regularly build large, complex BOMs—and then easily imports those data into your ERP.
• Nesting interface that automatically configures part shapes on bulk pieces of stock material to maximize use and minimize waste, and allows for two-way, bidirectional communication between your ERP and your nesting software.
• E-commerce integration, letting customers order and pay directly from your website and sending all job data to your ERP system to get the production process started. Integrating your website also lets your customers check on the status of orders and shipments without human interaction, saving you time and money, and giving them better 24/7/365 service.
• Integrated human resources and payroll significantly reduces HR personnel costs by managing employees and benefits in one system, enabling you to use a best-in-class partner of your choice.
For integrations to work, your ERP must be able to communicate with each third-party software and translate the information into your system’s language. If your ERP system doesn’t include these capabilities, it’s time to look for a new one.
Tailored ERP
Imagine having an ERP system built specifically for your business, one that lets you do everything exactly the way you need it done. ERP systems that let you tailor the software enable you to customize screens, programs, and processes to meet your exact needs, providing a real advantage in the race to do more with less. This includes adding or removing functionality, and automating processes to maximize efficiency and improve productivity.
The best way to turn data into information is with interactive dashboards that let you tailor the screens so they look and act exactly as you want.
Tailoring the way you organize and manage data offers a perfect example. In the manufacturing world, data are simply data until they become information. The best way to turn data into information is with interactive dashboards that let you tailor the screens so they look and act exactly as you want. Suppose your ERP system comes out of the box with a purchasing screen that displays 20 fields and six buttons, but you only need 10 fields and three buttons. With tailored ERP, you can reduce the “noise” by removing the unwanted fields and buttons so users only see the data they need to see.
Think of it this way. Your ERP software may come with dozens of screens built into the system, some of which you don’t need or don’t fit the way you do business. When you buy a new phone, you don’t put every application on it, only the ones you need. Tailoring ERP screens to your needs reduces distractions and makes it easier to find the data you want.
Some ERP providers offer two ways to tailor your dashboards. One is to build them from scratch using a dashboard designer program. This handy tool lets you pull real-time data from your ERP system to create custom layouts and grids that are easy to filter and sort. The program also includes custom widgets and visuals such as charts, pie graphs, sales and territory maps, gauges, and more.
The other method involves using a software development kit (SDK) to customize existing dashboards built into the software. This approach allows you to:
• Tailor screens for users and create applications specific to manufacturing processes that work with your ERP software.
• Change standard screens by removing or adding functionality to maximize efficiency for users.
• Create, schedule, and automate reports or workflow beyond what is included in your ERP’s standard applications.
• Pull data and functionality from several screens into one so you can work all day, every day, from a single screen.
When you need functionality beyond your ERP’s standard applications, the most flexible systems provide a full-featured software development tool that allows virtually limitless customization. With this tool you can customize and augment existing screens, create custom applications, automate a series of tasks, implement workflows, and much more.
These types of customizations often must be re-created when the ERP provider updates the software version. The best software development tools read and manipulate the data via business objects, so your customizations won’t break due to changes to the underlying data structure during version upgrades.
Interactive dashboards offer another important feature: They allow users to perform job tasks related to the information on the screen, such as receiving incoming materials or editing a work order in progress.
Until recently, performing job tasks in standard dashboards required clicking over to another screen and then back after completing the task. Interactive dashboards combine dashboard data with functionality in one screen. Instead of just reviewing data, you can perform everyday job functions directly from the screen to work faster and more accurately.
Eliminating the need to click on another screen may seem inconsequential. But when you consider how many employees click over and back dozens or hundreds of times a day, it can add up to significant time savings. When you need functionality beyond your ERP’s standard applications, the most flexible systems provide a full-featured software development tool that allows virtually limitless customization.
Add new comment