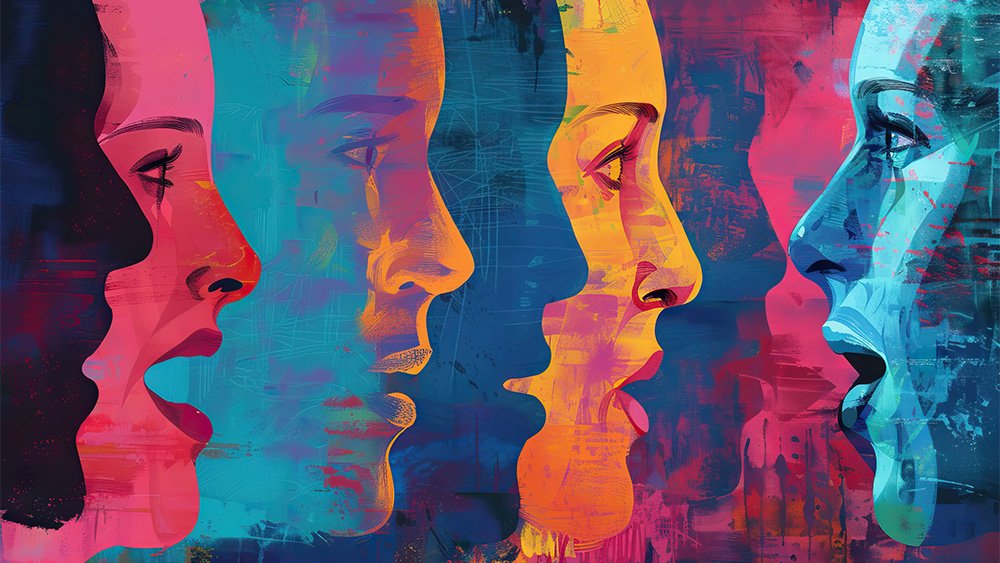
Adobe Stock
As a technology leader, I must admit that making the right investment in new innovations has its challenges. It’s easy to get caught up in the grandiose potential solutions offer, become overwhelmed by the setup, and struggle with employee adoption.
ADVERTISEMENT |
For the last decade, I’ve worked with human-centric industries like manufacturing and warehousing to determine what solutions can not only address business insight needs but also better support their employees. While the manufacturing industry has implemented digital transformation efforts in recent years, where I see the greatest technology gap is among frontline workers.
As the heartbeat of manufacturing, this group needs more intuitive, easy-to-use technology on the shop floor, including communication solutions. In fact, new research by Relay found that 82% of manufacturing and warehousing workers desire improved communication tools. Poor communication on the shop floor can result in many workplace concerns, from workplace safety issues to lost time and inefficiencies.
…
Add new comment