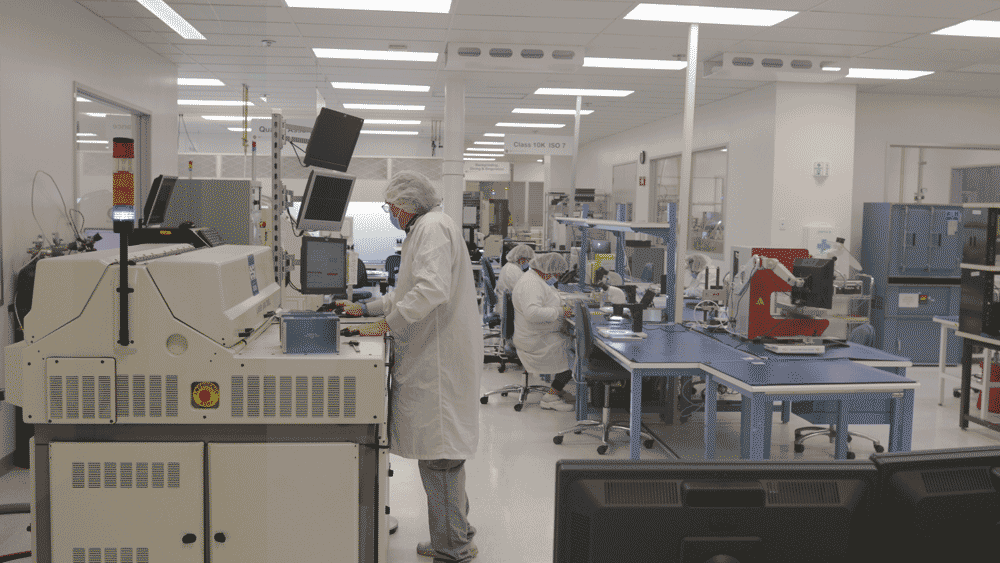
QP Tech
To meet the precise requirements associated with semiconductor manufacturing, integrated circuit (IC) packaging and assembly providers must navigate complex quality certification processes, such as those for the well-known ISO 9001 and ISO 13485 standards. Another important certification for facilities handling delicate electronic parts and components is ANSI/ESD S20.20.
ADVERTISEMENT |
Electrostatic discharge (ESD) is one of the most common and costly threats to semiconductor manufacturing. For companies involved in semiconductor packaging and assembly, controlling ESD is not optional; it’s essential. Many companies choose to formalize their protection efforts by obtaining certification to ANSI/ESD S20.20, a globally recognized standard. Here’s why ESD certification matters, and what’s involved in the process.
…
Add new comment