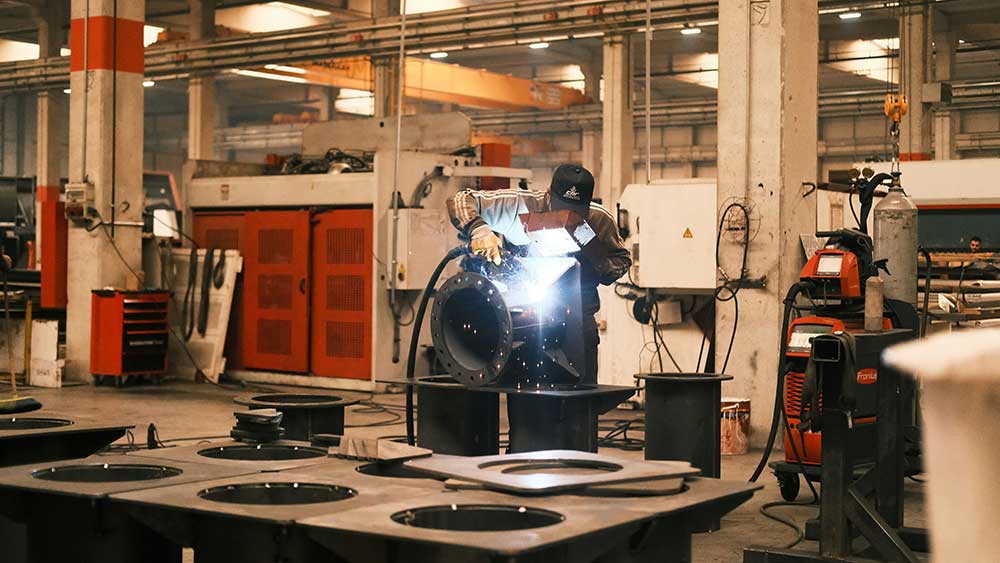
Photo by Cemrecan Yurtman on Unsplash
Paul was sitting in his office staring at production numbers from the past quarter. Despite having a great team, strong customer demand, and state-of-the-art equipment, the factory’s performance wasn’t meeting expectations. There was a bottleneck in the assembly line—a critical chokepoint that was slowing down the entire production process.
ADVERTISEMENT |
Paul had been working in manufacturing operations for years, but this bottleneck was something he couldn’t easily solve. Every time he thought they were close to a solution, a new issue popped up. The production targets kept slipping, and morale in the factory was starting to dip.
Paul wasn’t alone in this frustration. His team, especially the production manager, Sarah, had tried everything they could think of. They had streamlined workflows, optimized machinery, and even brought in extra shifts. But nothing worked. The assembly line still slowed down when they hit certain orders.
One afternoon, Paul was meeting with an operations consultant, Samantha, whom he had worked with on a previous project. As they sat in his office, the conversation took an unexpected turn.
…
Comments
More on TRIZ
Akhilesh,
While I think TAKT is a pretty well known and understood concept, I think you could share more about TRIZ and how to use the concepts for rapid continuous improvement. Perhaps you have in a previous post, but I am new to the discussion, and apologize if being redundant with my request.
Ken
Add new comment