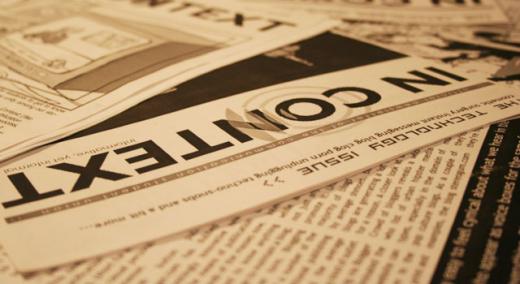
"in context" Credit: Erin Brown-John
In 2010, new to the world of statistical process control (SPC), I was intrigued by Don Wheeler’s statement that “No data have meaning apart from their context” (from his book, Understanding Variation—The Key to Managing Chaos, SPC Press, 2000, available on Amazon). For a while, I didn’t really get the importance of this message.
ADVERTISEMENT |
Now, some years later, and working mainly to support manufacturing processes, data analysis for me begins in context and ends in context. Moreover, communicating the results to others is driven by context, and the simpler this is done the better. To see an example, read on.
Time order of production
All, or practically all, manufacturing data have an essential piece of context, which is a time stamp. It’s the time stamp that allows you to put your data in a logical sequence—the time order of production—when you start the analysis.
…
Comments
Potential capability
“Potential” capability: The limits in figure 1 provide an approximation* of the capability to expect IF, and only IF, the assignable causes in this process are identified and effectively controlled.
The “IF” here is key: Without action on the assignable causes this “potential” capability has no meaning. Note the elephant in the room: No predictability = No actual process capability.
In this example, and because action on the assignable causes was planned, and did happen, the useful information in the potential capability was this: Achieve a predictable process and a capable process shall be expected. (This is because the limits in figure 1, 43.3-46.9, fall inside the specification range of 42.5 to 47.5.)
*This approximation is essentially an upper bound, but this point is secondary in the bigger picture of what capability means for an unpredictable process.
Add new comment