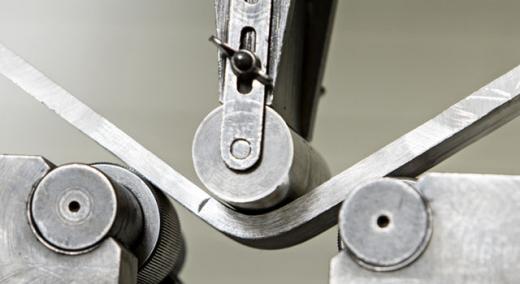
A lot of thought goes into building reliable assets. Extensive testing is a part of the process that has to be done to estimate the durability of machines, materials, and components. The testing can be done destructively or nondestructively.
ADVERTISEMENT |
In this article, we take a deep dive into the various aspects of destructive testing and its use cases.
What is destructive testing?
Destructive testing (often abbreviated as DT) is a test method conducted to find the exact point of failure of materials, components, or machines. During the process, the tested item undergoes stress that eventually deforms or destroys the material. Naturally, tested parts and materials cannot be reused in regular operation after undergoing destructive testing procedures.
Destructive testing is generally conducted before a component enters mass production. OEMs need to know the limits of their products in order to give proper maintenance and operating recommendations for their machines.
…
Comments
Residual Stress Destructive Testing
Bryan,
Your coverage of destructive residual stress measurement only refers to surface hole drilling. There are several other techniques available such as the contour method and deep hole drilling for through thickness measurement. The technique chosen depends on the requirement of the research. VEQTER Ltd are able to carry out all of these methods and others. Further details can be found here;
https://www.veqter.co.uk/
Add new comment